Due to high stresses and complex geometries, deep mining operations present unique stability challenges. Numerical modeling has emerged as an invaluable tool for simulating full-scale behavior, failure mechanisms, and interaction between layout geometries to facilitate the safe, sustainable, and economical design of deep excavations. This was highlighted in a recent study published in Mining.
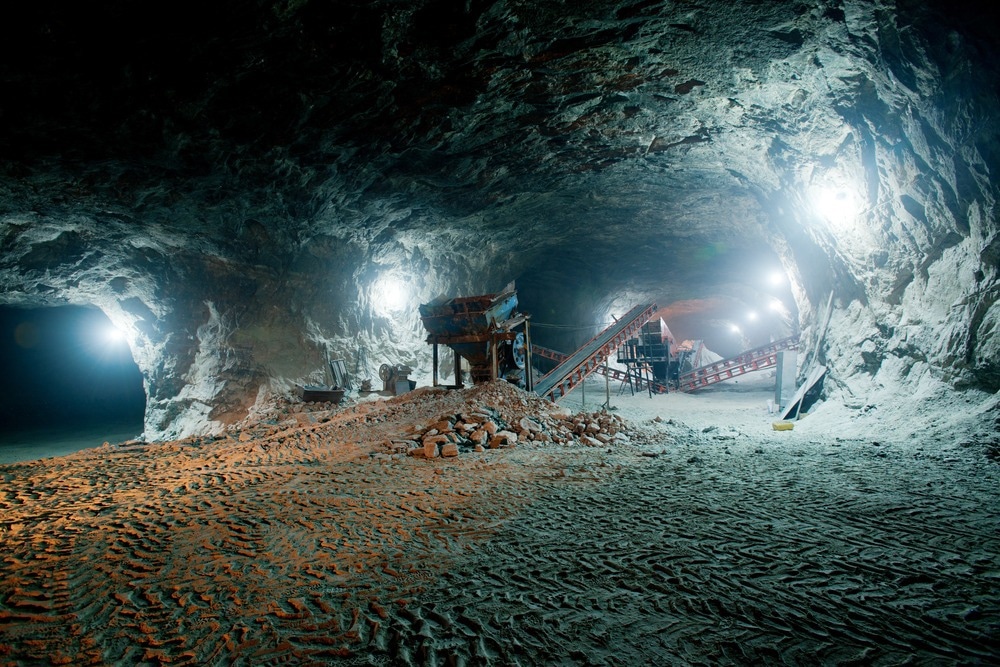
Image Credit: sezer66/Shutterstock.com
Need for Numerical Modeling in Deep Mining Excavations
The design and planning of underground excavations has always been a complex engineering challenge, but this complexity increases exponentially with depth as the magnitudes of in-situ stresses and rock mass deformation rise significantly. At higher depths, the tectonic stresses lead to violent failure conditions like rock bursts, squeezing ground, and slabbing, threatening operational safety and mining productivity.
At these depths, the rock mass undergoes complex mechanisms such as shear along structural planes, crack initiation, propagation, and coalescence, resulting in non-linear deformation. This cannot be solved using conventional analytical methods. Conventional stability graph solutions used in mining also lack the sophistication to simulate jointed rock mass behavior realistically.
Advanced numerical techniques, including the finite element method (FEM), boundary element method (BEM), and discrete element method (DEM), provide a robust modeling framework to simulate the true behavior of rock mass.
The DEM models discontinuous materials like rocks by representing them as interacting discrete elements, each with specific properties. It considers interactions through contact models like friction and cohesion.
The FEM discretizes rock structures into smaller elements for stress and strain analysis, assuming material continuity within each element.
The BEM models interactions between a rock structure's boundary and surrounding material or external forces, representing the boundary as surface elements.
Combining these models (hybrid) provides crucial insights, guiding engineers in designing optimized excavation spans, layouts, and sequencing to ensure safe mining operations.
Ongoing research focuses on improving these numerical models' accuracy, efficiency, and reliability, addressing challenges related to scale- and time-dependent changes in rock behavior.
Additional Advantages of Numerical Modeling for Deep Mining Excavations
Some significant advantages offered by numerical modeling include the following:
- Predicting ground behavior: Numerical models provide foresight into potential failure mechanisms, high-stress concentrations, and stability risks by simulating complex stress distribution and deformation around deep underground mining excavations.
- Hazard assessment: Realistic simulation of stress paths, rock mass yielding, and post-peak response enables the assessment of potential for hazards (such as rock bursts, coal pillar failures, and gas outbursts). This allows the implementation of suitable prevention and control strategies.
- Optimizing mine layouts: Numerical techniques that accommodate complex 3D geometries and coupled processes facilitate stabilization analysis and optimal layout configurations for safety and ore recovery in challenging ground conditions.
- Evaluation of support design: Modeling can quantify stresses, displacements, and strength factors along excavation boundaries under various loading scenarios. This facilitates appropriate sizing and optimization of rock support systems such as rock bolts, shotcrete lining, and cable bolts.
- Cost savings: While modeling requires expertise and computing resources, it saves significant time and expenses compared to physical testing of concepts, especially in extreme depths or large safety factors.
Case Study: Numerical Modeling for Deep Mining Excavation Stress Management
A recent study published in Mining effectively illustrates the advantages of numerical modeling in analyzing a rock engineering problem involving deep mining excavations facing high-stress challenges. The objective was to gain insights into stress concentrations, potential failure mechanisms, and deformation around the excavations.
The researchers simulated a complex rock mass structure by modeling interconnected parallel horizontal square tunnels while considering its mechanical properties, such as elastic modulus, Poisson's ratio, and tensile strength.
Lamodel and Examine 2D, boundary element code-based numerical modeling software, were chosen for their simplicity, quick usability, and suitability in solving deep mining problems.
Lamodel simulated stress and displacements, identifying concentrations and deformations around openings, aiding in designing supports, and indicating potential failure areas. Examine 2D assessed the displacement and stability along tunnel cross-sections.
The combined use of these models provided a comprehensive understanding of various rock mechanics phenomena, such as stress build-up leading to rock bursts, which are crucial for safe and sustainable mining operations.
Overall, this research highlights the practical importance of numerical modeling in understanding the stress influences in deep mining excavations, providing valuable insights that are challenging to obtain through manual testing.
Conclusion
Numerical modeling is an indispensable asset for deep mining excavations, offering unparalleled insights into complex stress distributions, failure mechanisms, and overall stability.
Its ability to simulate complex 3D scenarios, evaluate support designs, and facilitate proactive risk management positions are crucial for optimizing mine layouts and ensuring safe and sustainable operations in the challenging environments of greater depths.
References and Further Reading
Zvarivadza, T. (2023). Numerical Modelling Application in the Management of Deep Mining Excavation Stresses: An Illustrative Study. Mining. doi.org/10.3390/mining3040040.
Singh, GSP., Singh, UK., Murthy, VMSR. (2010). Applications of numerical modelling for strata control in mines. Geotechnical and Geological Engineering. doi.org/10.1007/s10706-010-9324-6.
Vikram, S., Kumar, D., Satya Subrahmanyam, D. (2022). Support System Design for Deep Coal Mining by Numerical Modeling and a Case Study. IntechOpen. doi.org/10.5772/intechopen.97840.
Castro, LAM., Bewick, RP., Carter, TG. (2012). An overview of numerical modelling applied to deep mining. Innovative Numerical Modelling in Geomechanics. https://doi.org/10.1201/b12130-22.
Hamman, ECF., Coulthard, MA. (2007). Developing a numerical model for a deep open pit. In Slope Stability 2007: Proceedings of the 2007 International Symposium on Rock Slope Stability in Open Pit Mining and Civil Engineering. doi.org/10.36487/ACG_repo/708_12.
Disclaimer: The views expressed here are those of the author expressed in their private capacity and do not necessarily represent the views of AZoM.com Limited T/A AZoNetwork the owner and operator of this website. This disclaimer forms part of the Terms and conditions of use of this website.