Sponsored by Firwin Corp.Mar 27 2024Reviewed by Aimee Molineux
Diesel-powered equipment plays a vital role in underground mining operations, from scoops and scalers to pallet handlers and personnel carriers, ensuring tasks are completed efficiently. Diesel power offers a rugged, reliable, and cost-effective energy source, accounting for 72 percent of the energy the mining sector consumes.1
Mining equipment manufacturers are currently faced with increasing demands as developing economies such as China and India are fueling extraction demand and contributing to the record high prices for aggregates, precious metals, and other natural resources. Therefore, there is a need to produce more diesel powered vehicles that have the ability to extract, load, and transport.
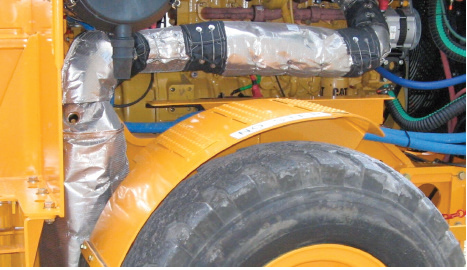
Mining Vehicle, Exhaust & Catalyst Insulated. Image Credit: Firwin Corp
Diesel-Powered Equipment in an Underground Environment: The Challenges
Underground mining presents many complex challenges, especially when it comes to the safe and efficient use of diesel-powered mining equipment in enclosed and confined spaces, some of which are listed below:
- Exposed exhaust and engine components: Diesel exhaust can get extremely hot, and working in an underground mine typically means working within confined spaces, which means workers are at increased risk of severe burns from uncovered exhausts and engine components.
- Diesel particulate matter: Exhaust from diesel-powered mining equipment must be filtered in the right way to protect personnel from inhaling toxic fumes.
- Fire Safety: Oil from a burst hydraulic hose or an engine leak can start to smoke if it comes into direct contact with exposed exhaust components.
- High ambient heat: The heat that diesel-powered equipment generates can heat up an already sweltering underground environment. This can put workers at risk as well as cause malfunctions in heat-sensitive cables and sensors.
Meeting the Challenges: How Insulation Blankets Can Help
Ensuring the right insulation is in place starts with blanketing exposed engine and exhaust components. This marks a key step in addressing the challenges associated with operating diesel-powered equipment in a mining environment. Once properly installed and insulated, ambient heat is reduced, and workers are at a reduced risk of overheating and being burned.
A good ventilation system is also vital to ensure that hot air is extracted and cooler air is pumped into the environment while eliminating any toxic or noxious fumes from the mine. Therefore, catalysts and particulate filters serve as crucial pollution control measures that can remove much of the noxious material before it is exhausted.
Good insulation can allow catalysts to burn exhaust pollutants more efficiently by maintaining an optimal high exhaust temperature as the exhaust travels along the piping and into the catalyst.
Standard Insulation Blankets: Why They Sometimes Fall Short
Standard insulation blankets have two main features, meaning they may not always be well-suited for underground mining:
The underside of a regular-issue insulation blanket is usually fabricated using a non-combustible fiberglass material held in position with wire mesh. While this assembly is suitable for most applications, certain scenarios in an underground mine can cause problems.
For example, should oil leak from a burst hydraulic hose line or an engine seep beneath an insulation blanket, it may become trapped within the insulation material. With only a wire mesh separating the hot component from this mixture of oil and insulation material, it presents a potential fire hazard, the last thing you want in an underground mine.
The second limitation associated with standard insulation blankets is the outer cover. Generally made of silicone-impregnated fiberglass, the outer cover is designed to be robust and endure normal wear and tear for years.
However, the harsh environment of an underground mine, characterized by confined spaces and the risk of rock falls, subjects the insulation blankets to numerous hazards. Heavy and sharp objects can easily come into contact with these blankets, which are not designed to withstand such treatment, leaving regular insulation vulnerable to tearing or puncturing.
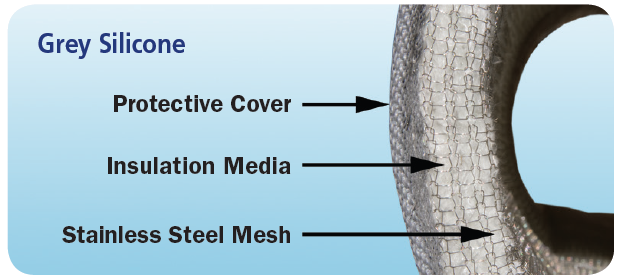
Standard Insulation Blanket Construction. Image Credit: Firwin Corp
MineWrap™ Insulation Blankets: Designed for the Underground Mine
To meet these specific concerns, Firwin’s R & D department developed a rugged blanket to meet the special demands of underground mining applications. Known as MineWrap™ Mark II, this blanket incorporates a stainless steel inner liner, which prevents any oil seepage by sealing off the insulation material.
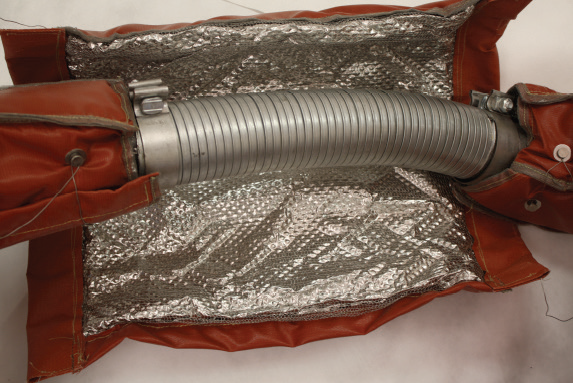
MineWrap Mark II’s Stainless Steel Inner Liner. Image Credit: Firwin Corp
For applications that demand even more strength and rigidity, MineWrap™ is available in a robust Mark III version.
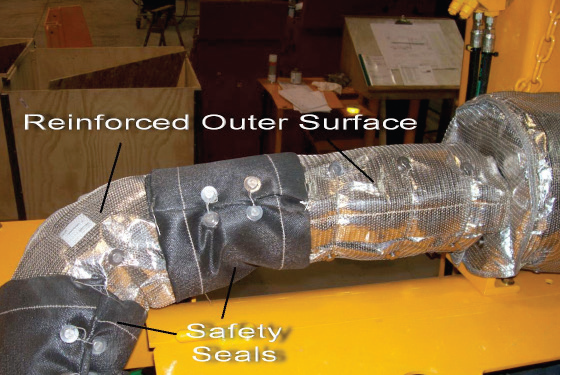
MineWrap™ Mark III Covering Exhaust and Catalyst. Image Credit: Firwin Corp
The Mark III blanket includes a reinforced stainless steel foil exterior covered with a stainless steel mesh. It is possible to add joint safety seals to seal off any additional areas of exposed exhaust between blanket sections. With increased fire safety and a rugged exterior, MineWrap™ is a common insulation blanket of choice for a number of mines and equipment manufacturers.
Firwin Hard Coat: A Permanent Insulation Solution for Underground Mines
A number of underground mines have come to the decision that while they require insulation for their hot exhaust components, they do not necessarily require removable insulation. These mines have thus opted for Firwin Corp’s Hard Coat™ insulation system. Hard Coat™ incorporates a durable, lightweight exterior and can be applied to components such as exhaust manifolds, elbows, turbochargers, and exhaust piping.
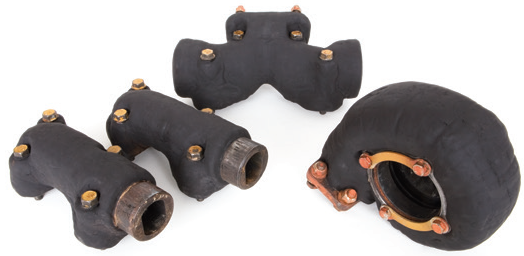
Firwin Hard Coat.™ Image Credit: Firwin Corp
In contrast to removable insulation blankets, which are fastened around an engine or exhaust component using a fastening system (usually stainless steel lacing wire), Hard Coat™ insulation offers a permanent insulation solution that is applied directly to the component.
This results in the component and insulation material being enclosed completely and protected from exterior elements. Therefore, the risk of equipment oil and fluid leaks seeping into the insulation material and causing a potential fire hazard is eliminated.
For certain high-temperature applications where safeguarding for oil leaks is a priority, space is at a premium, and a removable insulation product is not required, Hard Coat™ insulation is a definite option, and may be more economical in the long run.
Paul Herman, President, Firwin
While permanent insulation such as Firwin Hard Coat™ has its advantages, for instance it compactness and durability, there are drawbacks as well”, notes Paul Herman. “It cannot be removed should a part require servicing. The coating must be applied at our factory. It is also more expensive up front than traditional insulation blankets.
Paul Herman, President, Firwin
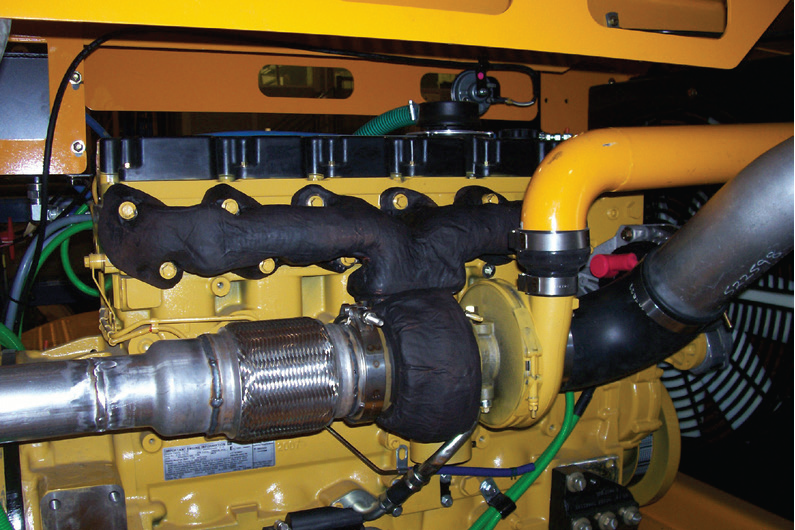
Turbo and Manifold with Firwin Hard Coat insulation. Image Credit: Firwin Corp
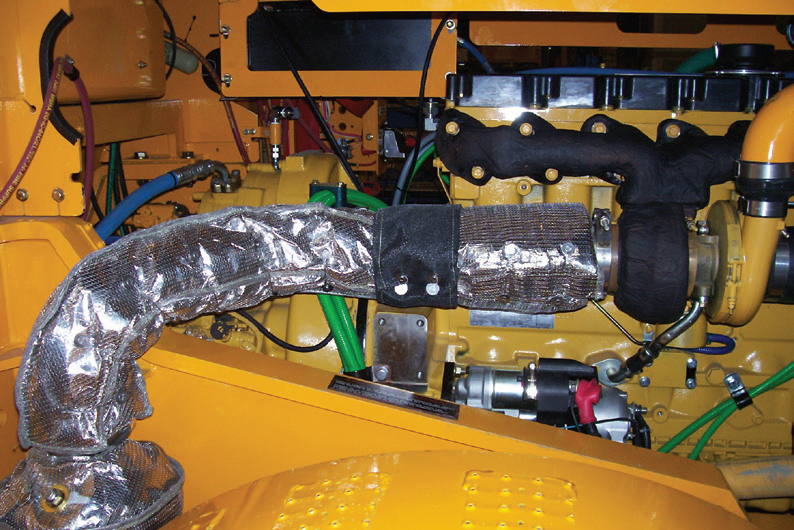
Mining exhaust with both MineWrap™ and Hard Coat. Image Credit: Firwin Corp
Conclusion
While insulating exposed hot exhaust components is essential for underground mines, selecting the appropriate insulation solution is crucial to ensure that the insulation itself does not introduce any new safety concerns.
MineWrap™ Removable Blankets and Hard Coat Composite Insulation have been developed to insulate mining equipment exhaust components effectively, taking all the major safety concerns of underground mining applications into account.
References
- Diesel Service and Supply website, Industrial_Industry_Usage
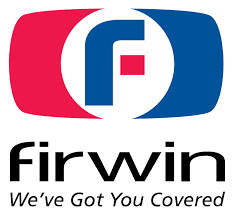
This information has been sourced, reviewed and adapted from materials provided by Firwin Corporation.
For more information on this source, please visit Firwin Corporation.