Grease makes heavy mining machinery work smoothly with minimal wear. Incorrect greasing leads to broken down parts, excessive rubbing wear, unexpected heat, and complete system failure. Keeping the correct amount of grease in the right places on an entire fleet of mining equipment is a task that is ripe for automation. Australian mining startup GreaseBoss was recently awarded for its innovative automated greasing platform at a mining industry ceremony.
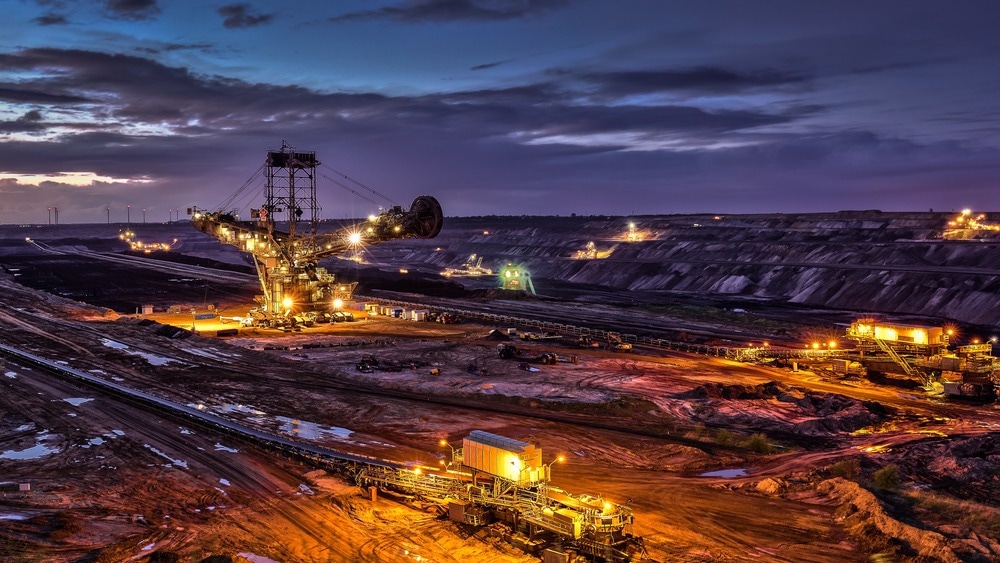
Image Credit: videomundum/Shutterstock.com
The Importance of Grease in Mining
Mining and other heavy industrial activities can run around the clock, and every minute of downtime results in significant financial losses for facilities operators.
In mining, 70% of production hours lost to equipment failure result from incorrect greasing.
Numerous mining machines require a correct application of grease to run correctly.
Fans that keep air flowing for worker safety have to operate continuously in wet and hot conditions. Electric motors drive machinery, but bearings problems related to incorrect grease levels make up 65% of all motor failures.
Conveyor belts keep everything moving and keep the mine productive, but often seals burst and bearings are destroyed due to over-greased parts.
Slurry pumps move a lot of pressurized material at high speeds. Grease is essential to prevent excess friction and wear, and to keep the unit sealed and contaminating material away from the bearing.
Excavators – heavy machines that chew through earth and rock – consume about 5500 kg of grease every month. These machines tend to have around 100 grease points each, with daily greasing and preventative maintenance required to make sure everything will continue to run smoothly. Haul trucks are even more significant, with over 160 grease points to manage.
Large mines may have hundreds of these machines on site. Too much or too little grease in any of the thousands of potential grease points across the mining fleet can halt production for the entire facility. Therefore, grease management is a large and important role in site operations.
Mining companies may have dozens or hundreds of sites worldwide. For these companies, finding a way to automate and more precisely control the application of grease to the entire fleet of heavy machinery can save billions of dollars in terms of reduced downtime and lower maintenance costs.
GreaseBoss’s Automated Greasing Platform for Mining
An Australian startup, GreaseBoss, is applying Industrial Internet of Things (IIoT) technologies – sensors, wireless connectivity, cloud computing, and artificial intelligence (AI) programs – to automate greasing for mining companies.
The GreaseBoss platform ensures that plant machinery is correctly greased, guides human workers to apply and record grease application, and provides dashboard functionality to site management.
The platform includes sensors fitted to traditional head units, endpoint units, and multi-end point units used to monitor grease levels in heavy plant machinery. Sensors can be installed on every greased part of the machine, ensuring that all nodes are covered in the data analysis.
Also included is a gateway system that provides wireless connectivity. This receives sensor data and transmits it to GreaseBoss’s cloud server. From here, GreaseBoss’s AI algorithms get to work making sense out of the large set of data being recorded by the sensors, spotting faults before humans could spot them, and ensuring the smooth operation of the system.
The platform also has a developer API, which enables mining companies to connect it with other enterprise software they use. For example, a company could connect the GreaseBoss platform with its automated stock ordering system, so there will always be enough grease available in stores to top up machines.
Award-Winning Product
GreaseBoss recently won the “Best Product Launch Award” in the Queensland Mining Awards, an industry awards ceremony for mining companies operating in Queensland, Australia.
Judges noted that the GreaseBoss system is the world’s first to track manual greasing on a point-by-point basis, with embedded verification that auto-lubricators are working.
GreaseBoss beats strong competition from finalists KAM Mining Products (for its track adjuster cannons) and Manuplex (for its dustless plaster pump).
Digitization is Driving Mining Forward
According to GreaseBoss, the predictive maintenance that this kind of digitization enables increases productivity by 35%, reduces breakdowns by 70%, and lowers maintenance costs by 25%.
It is not the first company to introduce automated greasing systems, although its innovation in automated data collection is disruptive.
Weir-Jones Engineering, a Canadian engineering company that provides goods and services to the mining industry, recently deployed an automated grease-dispensing system for tailings ponds equipment. The system can supply bearing and sealing greases to pumps under 70 m of water.
Researchers from Nigeria’s Benue State Polytechnic and the University of Agriculture recently employed artificial neural network (ANN) modeling to predict the viscosity index and specific heat capacity of various grease lubricants.
Their tests confirmed that the ANN, an application of AI, could accurately model these characteristics.
Outcomes such as these are a feature of the digitization trend in the mining industry. That trend is increasingly becoming mainstream as digital technology becomes more rugged, and novel uses of digital technology are proven to improve productivity in real-world mining conditions.
Smart Mining: The Benefits of Developing Digital Mines
References and Further Reading
2022 Winners. (2022) [Online] Queensland Mining Awards. Available at: https://qldminingawards.com/2022-winners/ (Accessed on 19 December 2022).
Leading The Digitisation of Greasing for Mining and Metals Operations. [Online] Greaseboss. Available at: https://greaseboss.com.au/mining-and-metals/ (Accessed on 19 December 2022).
Idoko, F.A., M.I. Oseni, and L.T. Tuleun (2017). Artificial Neural Network Prediction of Viscosity Index and Specific Heat Capacity of Grease Lubricant produced from Selected Oil Seeds and Blends. American Journal of Engineering Research. https://ajer.org/papers/v6(03)/ZC0603176181.pdf.
Weir-Jones Engineering Unveils Innovative Grease-Dispensing System. (2014) [Online] Mining.com. Available at: https://www.mining.com/web/weir-jones-engineering-unveils-innovative-grease-dispensing-system/ (Accessed on 19 December 2022).
Disclaimer: The views expressed here are those of the author expressed in their private capacity and do not necessarily represent the views of AZoM.com Limited T/A AZoNetwork the owner and operator of this website. This disclaimer forms part of the Terms and conditions of use of this website.