.jpg)
Image Credit: Peter Gudella/Shutterstock.com
The Bayer process is the cornerstone of global aluminum production. This involves refining the mineral ore bauxite to generate aluminum oxide (alumina), which gives aluminum when smelting1.
The Bayer process also creates an insoluble mixture of compounds known as Red Mud (RM), which, at present, is regarded as waste. Every year, the global aluminum industry generates approximately 120 million tonnes of RM2.
Multiple practical uses for RM have been studied, including making materials such as:
- Flooring tiles, lightweight aggregates, bricks, and cement
- Catalysis
- Ceramics such as sanitary ware, pottery, special tiles and glasses
- Soil conditioning
- Water decontamination
- Carbon dioxide sequestration
Most ends up in land-based depositories where it is often stored as wet slurry, or in the sea. If not properly managed, RM may pose risks to the environment as it is very alkaline (pH in the range of 13).
Depending on the make-up of the bauxites used in the production process, the chemical composition of RMs varies around the globe. It is chiefly made up of iron oxides and several elements and mineralogical phases, including calcium, silica, aluminum, and titanium1.
Other constituents may include chromium, copper, sodium, vanadium, lead, potassium, nickel, barium, manganese, and zinc. Organic compounds from decomposed vegetation may also happen as sodium salts of succinic, acetic and oxalic acids. Some others include polybasic and polyhydroxy acids, phenols and alcohols, and humic and fulvic acids.
Attention is now focused on the economics and feasibility of recovering valuable and useful minerals from RM such as aluminum, titanium, and iron. RM may possess considerable amounts of rare earth elements (REE), depending on the bauxite’s origin.
REEs may be extracted from RM by utilizing small molecular weight complexing agents (organic acids) and conventional agents (mineral acids)3. Some other methods include high gradient magnetic separators to recover iron.
Researchers must possess a detailed picture of the chemical composition of an RM sample before decisions on extraction and processing can be made.
X-Ray techniques are often used to study the elemental composition of substances due to the interaction of X-Rays with the electronic structure of the atoms.
One technique is to employ X-ray Fluorescence Spectroscopy (XRF), which is widely used for non-destructive, accurate elemental analysis in a large scope of applications. The range of elements studied by utilizing XRF typically spans from sodium to uranium.
Sample Preparation for XRF Analysis
Sample preparation is the key to gathering high-quality results with XRF, particularly for quantification of trace elements and low atomic number elements4.
Mineral composition, particle size, or density can all influence the intensity of the characteristic emission peaks and increase background scattering, and lighter elements can be harder to detect than heavier ones. The reliable quantification of sample composition can be difficult with these effects.
Samples can be ground, compressed and formed into smooth pellets before entering the machine to optimize the accuracy and reliability of results. This decreases scattering and enhances the detection of light elements.
By using a hydraulic press and a die set, pressed pellets are created. Typically, the sample is ground to a grain size of <75 µm then placed inside a pellet die. A pellet die consists of a hollow cylindrical body capped at one end at its simplest.
The die is put into a hydraulic press, which applies a load of several tons to the plunger, compressing the powder against the walls and base of the tube.The powder grains will bind to form a solid that can be removed if sufficient load is applied. Different loads are needed depending on the nature of the sample.
Specac’s Range
The Specac hydraulic press range includes manual, powered, and semi-automated Autotouch™ presses to cater for different sample handling needs.
Specac presses are capable of applying loads up to 40 tonnes for the Autotouch press and 25 tonnes for the manual and power presses.
For high throughput laboratories, the Autotouch with APEX Quick Release Die adds a level of automation to the press programming and pellet retrieval. These presses have fully programmable load and rest cycles which are accessible and customisable from a built-in touchscreen.
The power and manual presses are used for less intensive sampling routines in academic laboratories and occasional use in QC labs. They too can be used with the Apex die to simplify the pressing routine.
Specac also manufacture a range of more traditional hardened steel dies. For XRF analysis, die sets for 32 mm and 40 mm diameter pellets are recommended, but smaller sizes down to 5 mm are available for XRD and research-based XAS and EDX measurements.
References and Further Reading
- http://redmud.org/red-mud/production/
- http://homepages.see.leeds.ac.uk/~earitb/Burke%20et%20al%202012.pdf
- https://onlinelibrary.wiley.com/doi/abs/10.1002/jctb.5300
- https://www.specac.com/en/documents/application-notes/xrf-pellet-preparation
- https://www.specac.com/en/products/sample-preparation/hydraulic-press
- https://www.specac.com/en/products/sample-prep/dies
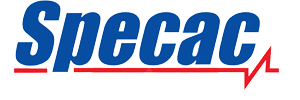
This information has been sourced, reviewed and adapted from materials provided by Specac Ltd.
For more information on this source, please visit Specac Ltd.