This article summarizes "The Electric Mine" report, highlighting key insights and notable company developments driving the mining industry's transition to full electrification.
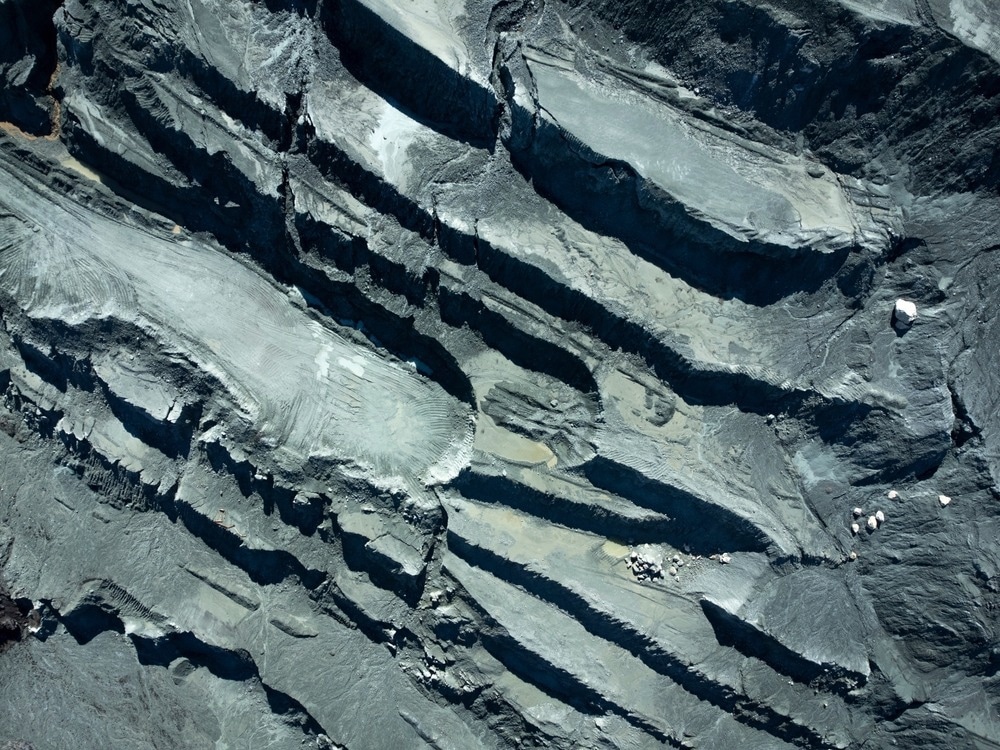
Image Credit: Savvas Karmaniolas/Shutterstock.com
Decarbonization Commitments Driving Electrification
Mining companies are charging full speed ahead with plans to electrify equipment and operations. This drive is fueled by ambitious net-zero emissions targets and facilitated by maturing technologies.
Leading mining companies recognize the urgent need to reduce emissions, aligning with the global shift towards clean energy. The sector currently contributes approximately 1 % to total greenhouse gas emissions. Notably, diesel-powered mobile equipment is responsible for 40-50 % of these emissions, while non-renewable electrical sources, such as coal and natural gas, contribute 30-35 %.
Substantial economic incentives are also driving this shift, as ventilation alone accounts for 30-50 % of underground mine energy costs, highlighting the significant impact of reducing diesel-powered equipment.
Mining companies with lower sustainability scores face 20-25 % higher capital costs. This makes electrification a strategic investment in the long run, aligning with the industry's commitment to both environmental responsibility and economic viability.
As a result, in 2021, a consortium of 27 major mining companies, as part of the International Council on Mining and Metals, committed to reach net-zero Scope 1 and 2 emissions by 2050. This commitment reflects a collective effort within the industry to address and mitigate the environmental impact of mining activities.
Technological Developments Enabling Widespread Mining Electrification
Advances in battery technology
Recent advancements in battery capabilities and charging systems have facilitated the swift rise of electrification over the last five years.
Traditionally, trolley systems were the primary method for electrifying haul trucks. However, in the 1980s, the Kiruna Electric Truck system revolutionized the industry. Commercial battery-powered trucks entered the scene in 2013, and by 2017, several original equipment manufacturers (OEMs) offered electric trucks and loaders. The momentum in electrification accelerated around 2018, marked by Epiroc's second-generation battery fleet launch.
At the end of 2022, mine operators had already deployed approximately 352 trucks with battery or hybrid technologies.
"Battery development has exceeded expectations," explained Mehrzad Ashnagaran, ABB's global product line manager for electrification and composite plants. "If you had asked us five to ten years ago, we could not have imagined where we would be today."
Larger haulage electrification solutions
The primary challenge for larger battery-electric haul trucks lies in designing a battery with the necessary energy density that can fit within the limited onboard space of the vehicle. However, significant progress has been achieved in expanding battery capacity to meet haul trucks' intensive energy needs.
For example, Williams Advanced Engineering, now under the ownership of Fortescue Metals Group, recently revealed a prototype battery system tailored for use in a Liebherr 240-ton haul truck. Additionally, Caterpillar has recently reported positive testing results for its first battery-powered 793 mining truck, which has a mammoth 265-ton haulage rating.
These developments demonstrate that mine-duty scale electrification is nearing commercial reality.
Fast charging connectors
Some experts point to ongoing enhancements in charging connector capabilities, which enable faster power transfer, as the most important breakthrough in accelerating adoption.
In 2021, ABB unveiled eMine, a comprehensive portfolio designed to seamlessly integrate battery-electric vehicles in mining. It includes charging products that prioritize energy efficiency and optimize overall performance for efficient operation.
The eMine portfolio incorporates fast off-board charging stations strategically placed across the mining area to support smaller haul trucks engaged in near-continuous operations with limited idle time.
Depending on the battery size (100-400 kWh for smaller haul trucks), charging times range from 6 to 24 minutes for 30 % to 90 % charge and 10 to 40 minutes for a full 0 % to 100 % charge.
Revival of trolley-assist systems
Trolley-assist systems are experiencing a resurgence as an interim solution for mine operators seeking to cut emissions from existing diesel fleets. These systems use hybrid diesel-electric trucks with a pantograph drawing power from an overhead trolley line, eliminating the need for diesel usage by 90 % while connected. This reduces emissions and offers substantial fuel cost savings.
According to ABB, converting one truck cuts CO2 emissions yearly, equivalent to the absorption of 46,000 trees, while trolley assist boosts loaded dump trucks on gradients, enhancing hauling efficiency.
ABB successfully implemented this system at Boliden's Aitik open-pit copper mine in Sweden, connecting four large diesel-haul trucks to a 700 m trolley line, and at Copper Mountain's flagship mine in British Columbia, Canada, linking seven diesel-electric haul trucks to a 1km-long trolley line.
In both instances, the trolley-assist system significantly reduced diesel consumption, leading to operator cost savings and a significant reduction in greenhouse gas emissions.
ABB is also pioneering combined trolley-battery solutions for larger electric mining trucks. This concept involves partial in-motion recharges from overhead trolley networks supplemented by onboard batteries.
ABB foresees this combined approach as "potentially being the better solution for larger trucks, while the smaller-sized trucks can operate as full battery-equipped vehicles with the off-board charging system."
Automating the electric mine ecosystem
Automation is the linchpin in optimizing the electric mine ecosystem by connecting and streamlining operations for increased efficiency, safety, and sustainability. It enables the deployment of autonomous vehicles, smart grids with renewable energy integration, and sensor networks for real-time monitoring and predictive maintenance.
Data analytics and artificial intelligence enhance decision-making, while robust communication networks facilitate remote control and safety measures. Automated systems also contribute to efficient supply chain logistics, making the electric mine ecosystem a seamlessly integrated and highly productive network.
ABB has been at the forefront of advancements in mining automation and control systems, as evidenced by its recent integration of automation and digital solutions practices in Kazakhstan, resulting in a doubling of capacity.
ABB's automated system Ability™ System 800xA monitors over 6,000 assets, optimizing maintenance, while crushers operate unattended from a control room in Canada. In Germany, ABB facilitates fully automated bulk material terminals, and in Sweden, their trolley assist electric truck infrastructure includes digital cargo tracking.
The company's automated ventilation platforms at the Boliden Kankberg gold mine in Sweden yielded over 50 % energy savings through real-time airflow adjustments in deep underground mines, significantly enhancing working conditions.
Alternative zero-emission drivetrains
Although behind battery-electric technology, hydrogen technology is being trialed at certain mines, such as Anglo American's Mogalakwena platinum mine in South Africa, indicating a growing interest in alternative solutions within the mining industry.
Liebherr showcased its expertise in hydrogen engines at Bauma 2022, winning the innovation award in the climate protection category for its H966 hydrogen-powered excavator. Liebherr is now exploring the potential of these engines to run on ammonia, with testing in an internal combustion engine anticipated in the near future.
Electrification's Costs Versus Benefits
Mining technology experts advise that fully electrifying operations may not represent the optimal decarbonization solution or deliver favorable economics at every mine site. While suitable for new mines designed with electric drive equipment in mind, retrofitting existing facilities poses considerable challenges regarding layout and infrastructure.
Customers exploring electrification options should balance expected emission reductions with infrastructure expenses. For instance, Epiroc recorded major performance gains from electrifying models—energy savings of 70 %, 25-30 % lower preventative maintenance costs, 10 % productivity boosts, and noise reduction.
A thorough analysis is therefore crucial to determine if electrification yields sufficient reductions in carbon emissions and operational costs, justifying the capital expenditure.
Partial electrification
Since rapidly transitioning from diesel to electric operations remains extremely challenging, ABB suggests a gradual integration approach. Beginning with a small initial fleet of battery trucks allows miners to lower emissions while gathering operational experience.
This approach allows for gradually scaling up electric haulage and infrastructure in manageable phases, aligning with technology improvements and budget availability.
"A phased approach enables mines to immediately lower carbon footprints with a limited up-front capital investment while advancing progressively as technology becomes more mature, scalable and cost-effective." Mehrzad Ashnagaran.
Industry Collaboration Drives Standardization and Interoperability
The specialized demands of adapting battery and hydrogen solutions for intensive mining applications have galvanized increased collaboration between vehicle OEMs, charging/power vendors, and end customers. Aligning technical standards and control interfaces for safety, efficiency, and fleet flexibility represents a key focus area.
One prominent example is the Global Mining Guidelines Group, which actively shares underground mining electrification best practices across industry stakeholders. In July 2022, the organization published extensive recommended practices spanning mine layouts, electric vehicle designs, battery technologies, charging methods, and performance metrics.
Standardized equipment
Mining companies increasingly demand standardized charging infrastructure to enable flexibility across various OEMs. This allows mines to choose battery-powered haul trucks and loaders from different suppliers while ensuring compatibility with shared recharging systems.
For example, Glencore aims for its Ontario-based Onaping Depth nickel-copper underground mine to be one of the world's first fully electric mines. To achieve this, Epiroc will provide universal CCS Type-1 chargers, ensuring seamless integration of mixed-brand electric fleets with a priority on interoperability to avoid vendor lock-in.
However, enabling multi-OEM equipment interoperability requires adopting universal connector standards for seamless integration with shared high-voltage infrastructure. ABB advocates collaboration between OEMs and technology providers such as Hitachi, Liebherr, and Komatsu to align their offerings with comprehensive site-wide electrification, automation, and digitization systems.
These collaborative approaches are instrumental in addressing the complexities of integrating diverse equipment seamlessly into a shared high-voltage infrastructure.
Conclusion: Steady Transition Toward All-Electric Mines
The in-depth industry report highlights a strong push towards developing fully electric mines, with collaborations between miners, OEMs, and specialized players addressing technological challenges. The consensus is that a gradual transition into integrating more battery and automation technology minimizes risk for miners. Full electrification is expected to become widely adopted in the next decade as technologies advance.
References and Further Reading
Nadav Shemer. (2023). The Electric Mine. [Online]. Aspermont Media. Available at: https://www.miningmagazine.com/digital_assets/460cd795-ac74-4df7-b748-9bfed7ae7a6d/The-Electric-Mine-Report-MM-AMM.pdf
Disclaimer: The views expressed here are those of the author expressed in their private capacity and do not necessarily represent the views of AZoM.com Limited T/A AZoNetwork the owner and operator of this website. This disclaimer forms part of the Terms and conditions of use of this website.