In this third in a series of Q&As, Ellen Thomson, Senior Product Application Specialist at Thermo Fisher Scientific, discusses the opportunities for process optimization across the concentrator, and strategies that can help miners improve cost efficiency, while at the same time driving down environmental impact.
Can you highlight the areas of the concentrator where there are the most opportunities for optimization?
Yes, the grinding circuit is an area where optimization can have a significant impact.
More than 50 % of the energy consumed at a mine goes into crushing and grinding. This is an essential first step in metal liberation, but often the process control in the grinding circuit is not optimized. This is because there is no clear understanding of what the target particle size should be for a given head grade, and no robust control strategy in place to achieve it. When you consider the relationship between particle size and energy consumption, and the importance of optimizing the particle size, then the economic and environmental impact of overgrinding is clear. But coarser particle size means lower metal recovery. Therefore, it’s a balance, and it’s vital to find the sweet spot for any specific mine or ore, accounting for all relevant factors, including milling media consumption and downstream processing requirements. Furthermore, in flotation, excess fines can drive up reagent consumption.
That brings us to the second key area, which is the flotation circuit. Flotation is a complex physicochemical process. Reagents – such as frothers, collectors and pH modifiers – are used to boost separation performance, but process levers are also utilized to manipulate feed rate, aeration rate and pulp density. The incoming feed may vary in terms of particle size – depending on grinding circuit control – and chemistry. A rational response to this complexity is reagent overdosing, but this can have a detrimental effect on performance. Learning how to optimally dose in response to incoming grade and particle size can result in cost savings, as well as reduce the environmental impact.
Lastly, I’d highlight the opportunities around concentrate sales and management. Certain impurities compromise the value of concentrate and, too often, they’re not properly monitored. The worst case scenario is the rejection of a delivered concentrate. But more generally, better monitoring can be a route to improved pricing and reputation, along with reducing the risk of penalty charges.
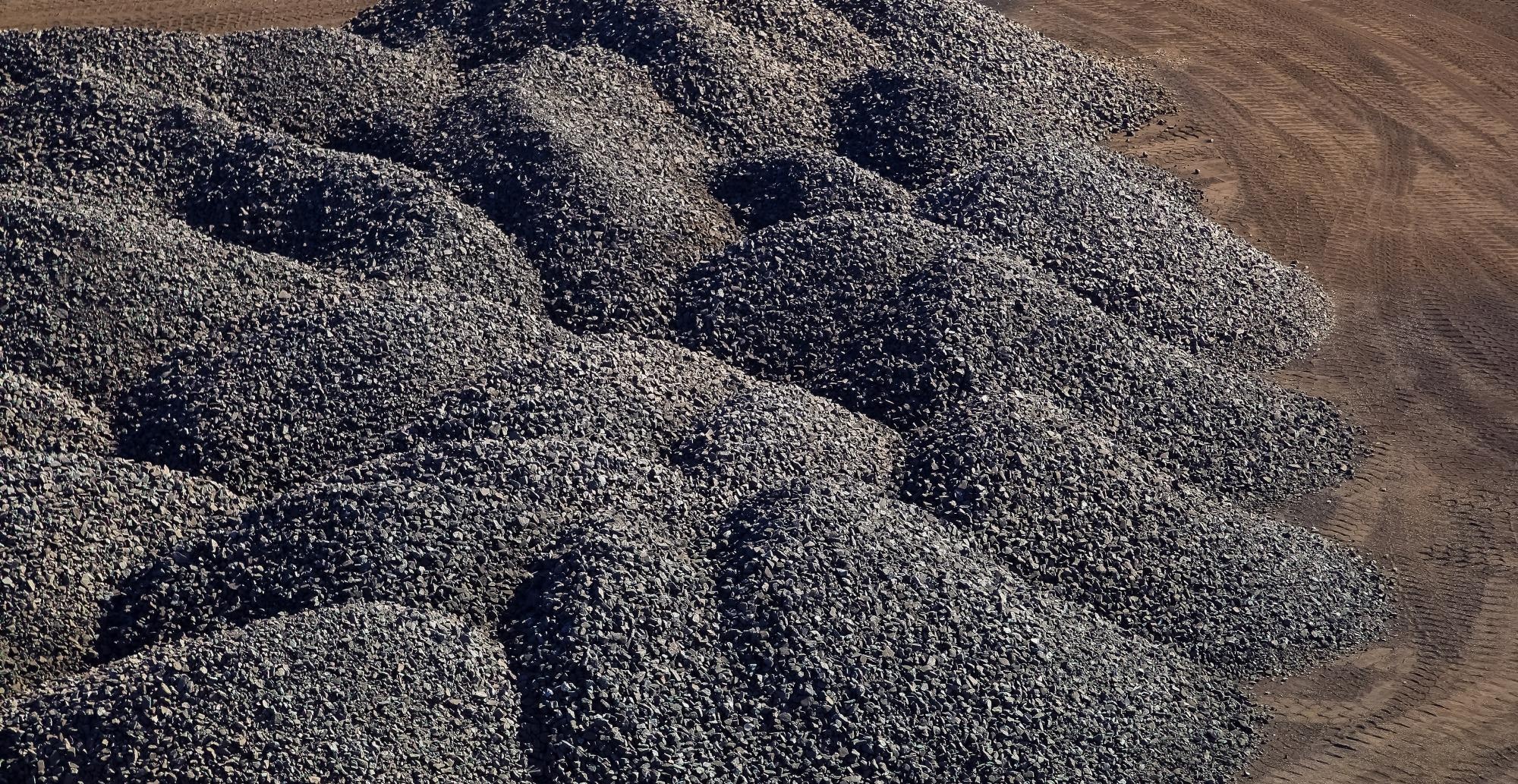
Image Credit:Shutterstock/SunshineSeeds
What is the main limitation with respect to process improvement?
Lack of reliable information.
Improving the performance of any process relies on understanding why it is operating sub-optimally. It’s vital to identify and quantify the cause and effect; if I change this variable, what is the effect on this parameter of interest?
In manually operated processes, operators address these issues routinely and automatically with varying degrees of success. The most experienced operators often have highly developed insights into the impact of a process change, established over many years. But without reliable, timely feedback, control is always going to be on a ‘trial and error’ basis. That’s simply not good enough for accessing the levels of performance that miners are now looking to achieve.
Where do people go wrong when it comes to selecting an analytical solution?
One of the most common mistakes is not giving sampling the consideration it deserves. Reliable, representative sampling is the foundation of any measurement, but multiple issues make it particularly demanding for miners, such as concentrated slurries and high tonnages, the long distances between analyzer and sampler, and the expense and complexity of tackling head constraints. It’s particularly important to recognize the potential pitfalls of multi-stream samplers, as they can be an excellent, cost-effective solution, but they have their limits.
It's not unusual to see multi-stream analyzers handling 12 or more streams where less than half of them are working. A centralized sampler of this sort is probably going to be associated with considerable slurry transport, and it’s very easy for lines to block. Also, every stream added into a multi-stream sampler system means longer times between results, and by extension, less responsive control. Multi-stream samplers have their place, but too often they exemplify the classic mistake of being drawn into a low, upfront cost without proper consideration of the long-term implications.
The other point I’d make is that any analytical solution for mining needs an established track record of high reliability with minimal manual input. Examine exactly what a vendor is offering in terms of proven availability, and look carefully at the routine maintenance requirements.
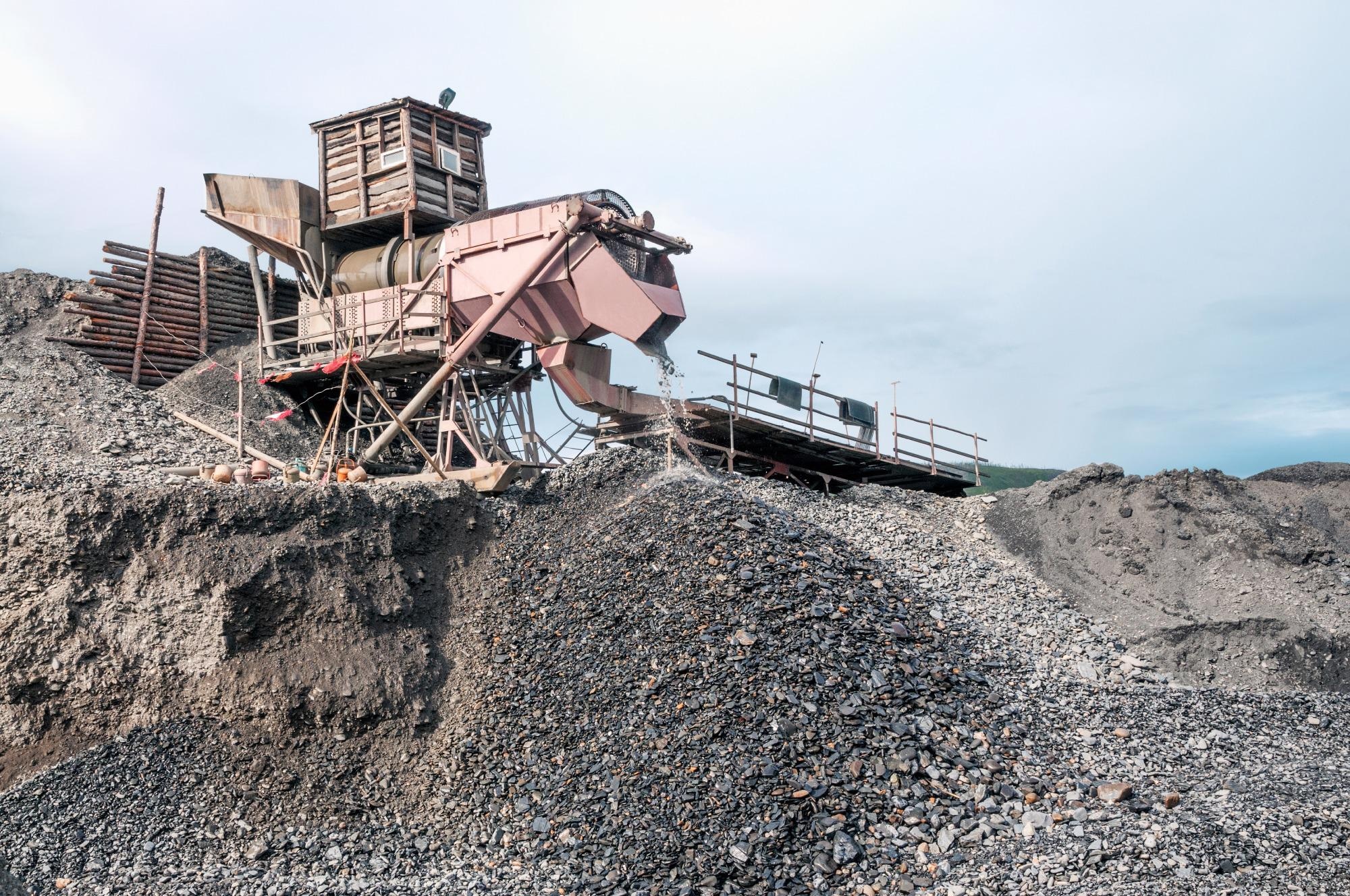
Image Credit:Shutterstock/LETOPISEC
What are the most productive strategies for maximizing ROI on an analytical system?
One is to think carefully about what you’re going to measure and why. The streams that make up the metallurgical balance are a good place to start when it comes to investing in analytical systems. Measuring how much recoverable copper is coming out of the mine and where it goes – how much ends up in concentrate (product) relative to tailings (waste) – allows you to follow the dollars through the process. All stakeholders are interested in these metrics, making reliable and good quality data highly valuable.
More generally, it is helpful to think about what you would do with specific analytical data if you had it. What actions would be based on the values? It’s also important to differentiate between opportunities where measurements could drive an automated control loop and those where a periodic check is all that’s needed. This will help with identifying the highest value opportunities, and selecting a suitable solution.
It can also be beneficial to get some expert help. If you’re working on a greenfield site, addressing analysis from the outset is crucial, and getting professional input can help integrate it effectively into your layout/flowsheet. On the other hand, expert guidance in an established facility can be the key to achieving a cost-effective solution within the unique constraints faced.
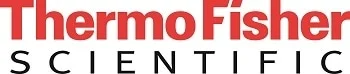
This information has been sourced, reviewed and adapted from materials provided by Thermo Fisher Scientific – Solutions for Industrial and Safety Applications.
For more information on this source, please visit Thermo Fisher Scientific – Solutions for Industrial and Safety Applications.
Disclaimer: The views expressed here are those of the interviewee and do not necessarily represent the views of AZoM.com Limited (T/A) AZoNetwork, the owner and operator of this website. This disclaimer forms part of the Terms and Conditions of use of this website.