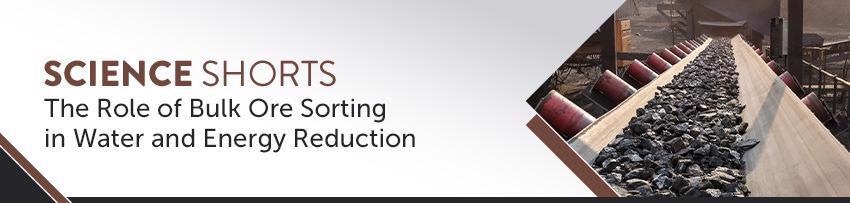
Lane, Hille, Pease & Pyle introduced their paper titled ‘Where are the Opportunities in Comminution for Improved Energy and Water Efficiency?’ at a recent SAG Conference event.
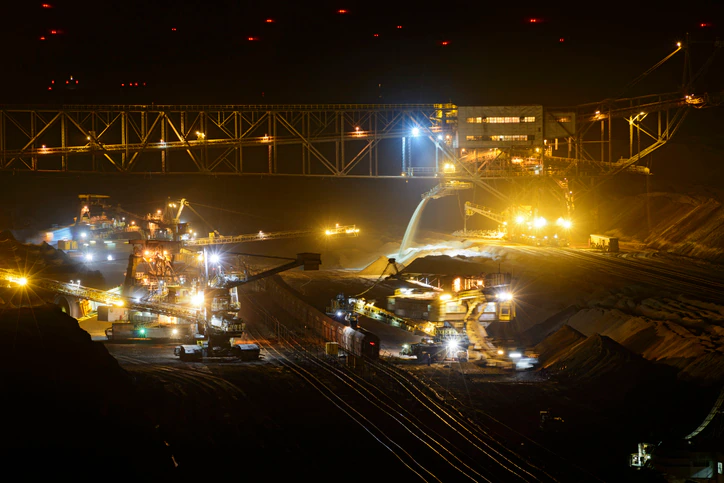
Image Credit: Thermo Fisher Scientific – Solutions for Industrial and Safety Applications
The SAG Conference is an excellent networking and information-sharing opportunity for anyone working with autogenous, semi-autogenous and HPGR grinding applications in the metalliferous and industrial mineral industries.
The paper detailed how a combination of the cost of energy, the availability and cost of water and community attitude have prompted mining houses to explore how to improve energy and water efficiency.
The paper also listed some notable and recent shifts in the inputs used to choose the most appropriate comminution circuit - whereby ore is broken down into smaller packages.
The authors stated: “Both energy and water efficiency are potentially vastly improved by the application to the minerals industry of the emerging sensing and sorting technologies. First prize is to reduce the waste reporting to the first level of comminution through bulk sorting prior to or just after primary crushing, through shovel and bulk belt sensors.”
Similarly, the 8th Edition of Wills’ Mineral Processing Technology by Barry A. Wills and James Finch highlighted that “Comminution consumes the largest part of the energy used in mining operations, from 30 to 70% (Radziszewski, 2013b; Nadolski et al., 2014).”
“This has consequently drawn most of the sustainability initiatives designed to reduce energy consumption in mining, including, for example, the establishment of CEEC (Coalition for Eco-efficient Comminution) and GMSG (Global Mining Standards Guidelines Group).”
Bulk ore sorting is a key means of addressing these areas of concern. The concept of ore sorting is broad, frequently including sorting by particle size, grade and mineralogy across various mineral processes.
The installation of an on-line elemental analyzer facilitates early, accurate measurement of material grades transferred to the process plant. This allows users to make an informed decision on material that is below target grade, redirecting this to a waste stockpile or specific low-grade process.
Since the plant is able to bypass or divert material that may be detrimental or not economically viable to the process, it is able to reduce water, power and reagent use.
A typical flotation plant requires up to 700 l/t of water for processing, meaning that processing fewer low-grade materials and thereby generating less waste will result in a reduction in the use of water, which in turn can reduce the cost of water supply or the cost of operating a desalination plant.
This also reduces the costs of water filtering at the end of a process, as well as limiting the amount of water that reaches a tailings dam.
Grinding and crushing of ore is an energy intensive process, accounting for around 3-5% of the world’s power usage. For every ton of waste not processed, there is a notable reduction in comminution costs, as well as a reduced impact of wear on equipment and subsequent maintenance costs.
Early waste rejection has the potential to reduce the footprint and capital expenditure related to the processing plant and tailings dam.
Declining ore grades can result in a reduction of revenue where a plant is operating at maximum throughput. Proper ore sorting allows a plant to improve the average grade of ore being processed, therefore maximizing rates of metal recovery.
Historically, the solution to this issue has been an increase in capacity in order to offset this via large capital investment and additions to plant infrastructure. Bulk ore sorting offers the potential to either delay or wholly eliminate the need for this capital spend while also ensuring that high grade material is delivered to the mill.
The increased recovery and profitability from bulk ore sorting can extend mine life, increase return on investment and delay expensive site rehabilitation.
The potential benefits of bulk ore sorting are greater than simply a reduction in water and energy consumption.
Acknowledgments
Produced from materials originally authored a Thermo Fisher Scientific representative.
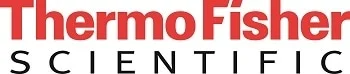
This information has been sourced, reviewed and adapted from materials provided by Thermo Fisher Scientific – Solutions for Industrial and Safety Applications.
For more information on this source, please visit Thermo Fisher Scientific – Solutions for Industrial and Safety Applications.