Light microscopes (LM) and scanning electron microscopes (SEM) are regularly used for mineral liberation studies to measure the accessibility of minerals relative to the recovery process, as well as provide information on the quality of the feed and the subsequent processing.
An absolute necessity when conducting the analysis is ensuring that the sample be prepared in a manner compatible with the microscope in use. Sample preparation should not be seen as an inconvenience imposed by lab equipment but rather as a key step to ensure and maintain the quality of the results and the inferences acquired. Poor sample preparation may cause density stratification, plucking, doming, agglomeration, pitting, and insufficient surface exposure.
As well as issues with mechanical sample preparation, the analysis can be restricted to the exposed surface of the mineral and therefore affected by stereological limitations and the presumption that the exposed surface is representative of the entire sample and a valid description of the particles present. Regardless of whether the analysis is conducted on the LM or with automated mineralogy (AM) software on an SEM, each of these issues may compromise the analyses of the modal mineralogy, grain size, liberation, and associations information.
In recent years, there has been a development of techniques that ensure a representative sample devoid of sample preparation artifacts is presented for analysis. For instance, the introduction of graphite to the sample to stimulate particle separation and prevent density stratification, and the analyses of particles to sufficiently describe a set of average particles and reduce any limitations stereology may impose (the interpretation of 3D samples based on 2D information).
Overall, sample preparation is a time-consuming activity, which may take around 24 hours to complete, and incorporates a series of meticulously taken steps starting with material acquisition before moving to the later stages of resin block setting, grinding, polishing, and coating with a conductive layer.
None of the steps can be bypassed, guaranteeing reliable data. This article describes the paradigm shift in automated mineralogy that addresses the need to understand a 3D world by analyzing it on 2D surfaces.
Mineralogic 3D – Automated Mineralogy
ZEISS Mineralogic 3D utilizes 3D X-ray microscopy techniques and deep learning algorithms to perform automated mineralogy analyses in three dimensions (fig 1). This helps deliver particle identification, mineral classification, and data outputs, including liberation and association measurements.
Conducting 3D analysis has three immediate benefits:
- Simplification of the sample preparation process
- No stereological assumptions as every grain is viewed in its entirety
- Significant reduction in the time to actionable data
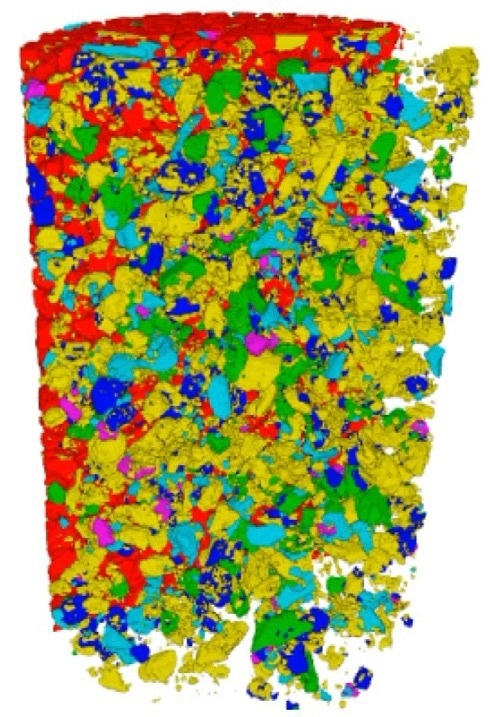
Figure 1. Analysis of a comminuted ore with the 3D X-ray microscope reveals the true mineral liberation with no mineral hidden by lack of exposure. Image Credit: ZEISS Raw Materials Group
Analytical Considerations
Sample preparation
Sample preparation for Mineralogic 3D analysis is relatively simple when compared to the laborious sample preparation workflow that must be followed to ensure valid data from SEM analysis of a comminuted sample.
All that is required for 3D analysis is a container or tube that can hold the sample and a stopper at either end to help keep it in place.
A step of complexity has been incorporated by introducing a technique that enables the mounting of several samples in the same sample carrier (tube). However, this is still comparatively straightforward considering the intricacies of graphite addition, mix stirring, setting, grinding, and polishing expected for the SEM analysis. The result is a streamlined workflow that saves several hours.
Adding graphite to the sample keeps particles apart, aids the assessment of liberation and associations, and deters gravitational settling in the samples. Gravitational settling is not a concern since Mineralogic 3D views the whole sample, including minerals locked within the particles.
Particle separation is dealt with by the machine learning protocols for segmentation. This determines the individual status of each particle as independent from other particles with which it may be in contact (Figure 2).
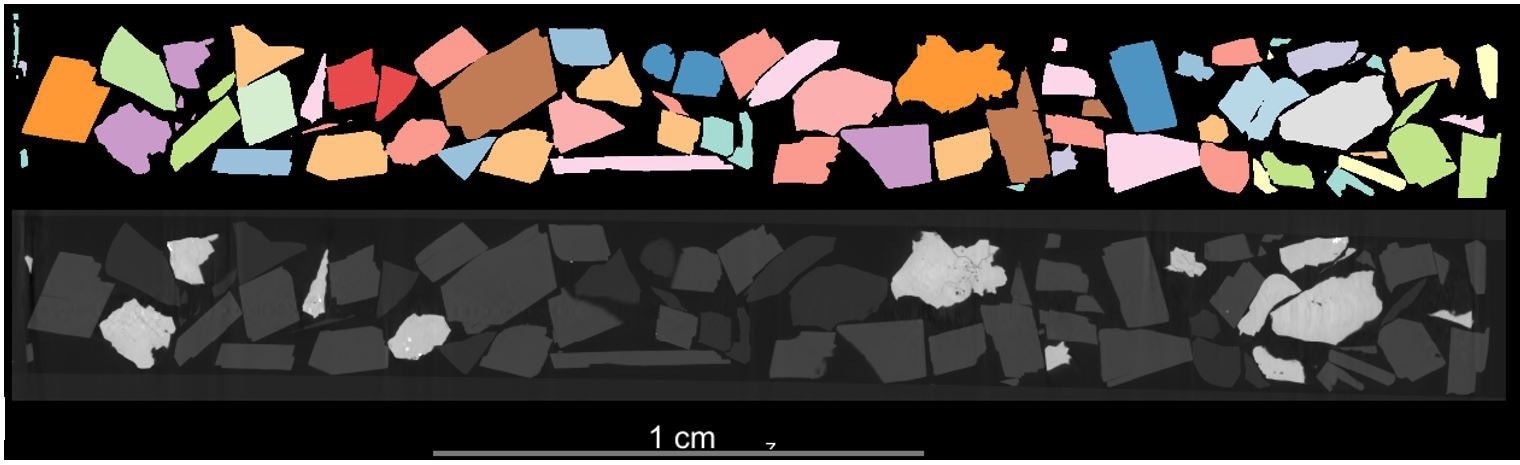
Figure 2. Longitudinal cross-section of a 3D scan of ground material. The coarseness of the particles provides a clearer example of the ability of the machine learning protocol to automatically identify and separate particles from each other. Image Credit: ZEISS Raw Materials Group
Mineral Classification and Time to Actionable Data
Taking full advantage of the imaging capability of the ZEISS Versa X-ray microscopes or ZEISS Context microCT, boosted by the introduction of DeepRecon noise reduction deep learning algorithms, Mineralogic 3D classifies the mineralogy of the sample automatically based on attenuation measurements (Figure 3).
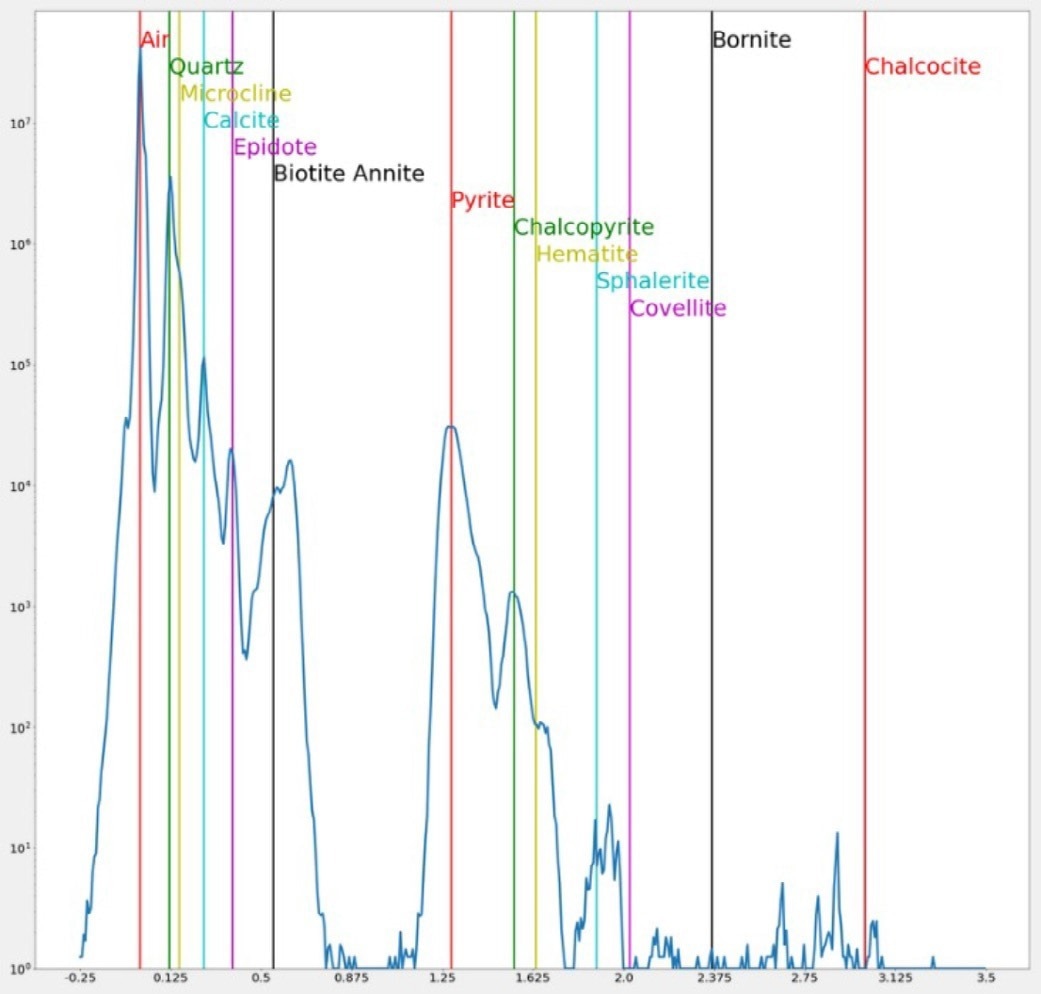
Figure 3. Mineral classification based on beam attenuation measur ements. Image Credit: ZEISS Raw Materials Group
The unique capacity to classify the mineralogy in tomographic scans, in combination with the morphological measurements of the 3D reconstructed entities, enables the calculation of conventional mining relevant outputs, e.g., morphological parameters, associations, and liberation.
The capacity to be able to measure the surface of particles as well as their interior mineralogy adds significant value to the data generated. When evaluating the value of the data, it is worth considering the time lapse between asking a question of the sample and gaining access to an answer. For instance, if the data provokes an action rather than an understanding, then it must arrive within the window of opportunity for which it can be actioned.
Taking complete advantage of the streamlined sample preparation workflow, Mineralogic 3D offers access to actionable data in far less time than metallographic preparation requires for the SEM.
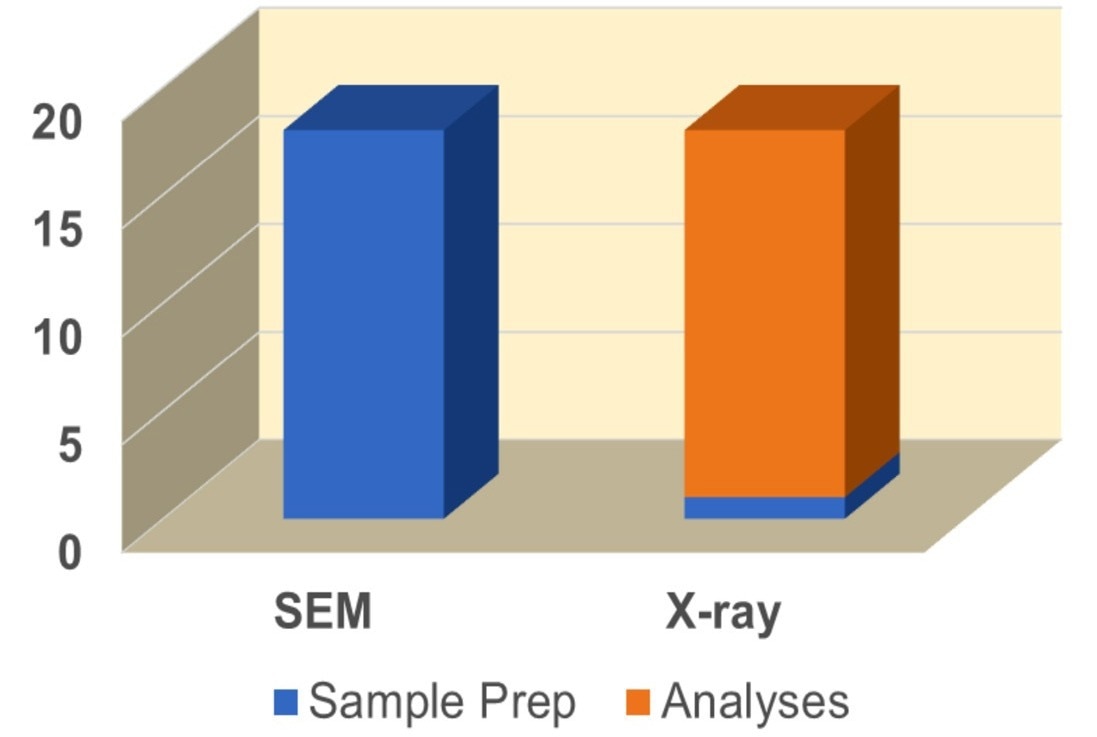
Figure 4. The simplicity of sample preparation combined with advanced analytical techniques results in a marked time savings in results delivery with Mineralogic 3D. Image Credit: ZEISS Raw Materials Group
Measurements
Once analysis is complete, Mineralogic 3D immediately reports on modal mineralogy, liberation, associations, particle and grain size, etc. All measurements should be, in theory, familiar to users of automated mineralogy on the SEM. However, it should be noted that there are some slight differences of relevance between the two techniques.
Sample Exposure
Particles must be fixed in resin block, which is ground and polished to expose suitable particle sections when conducting automated mineralogy on the SEM.
Grinding and polishing mechanically alters the sample and exposes only a fraction of the particles and mineral grains present.
Conversely, Mineralogic 3D does not mechanically alter the sample, and every grain in the sample is visible to the analysis.
Modal Mineralogy
Modal mineralogy accounts for the volume of each phase present in the sample. There is no need for it to be exposed on the surface to be accounted for (Figure 5).
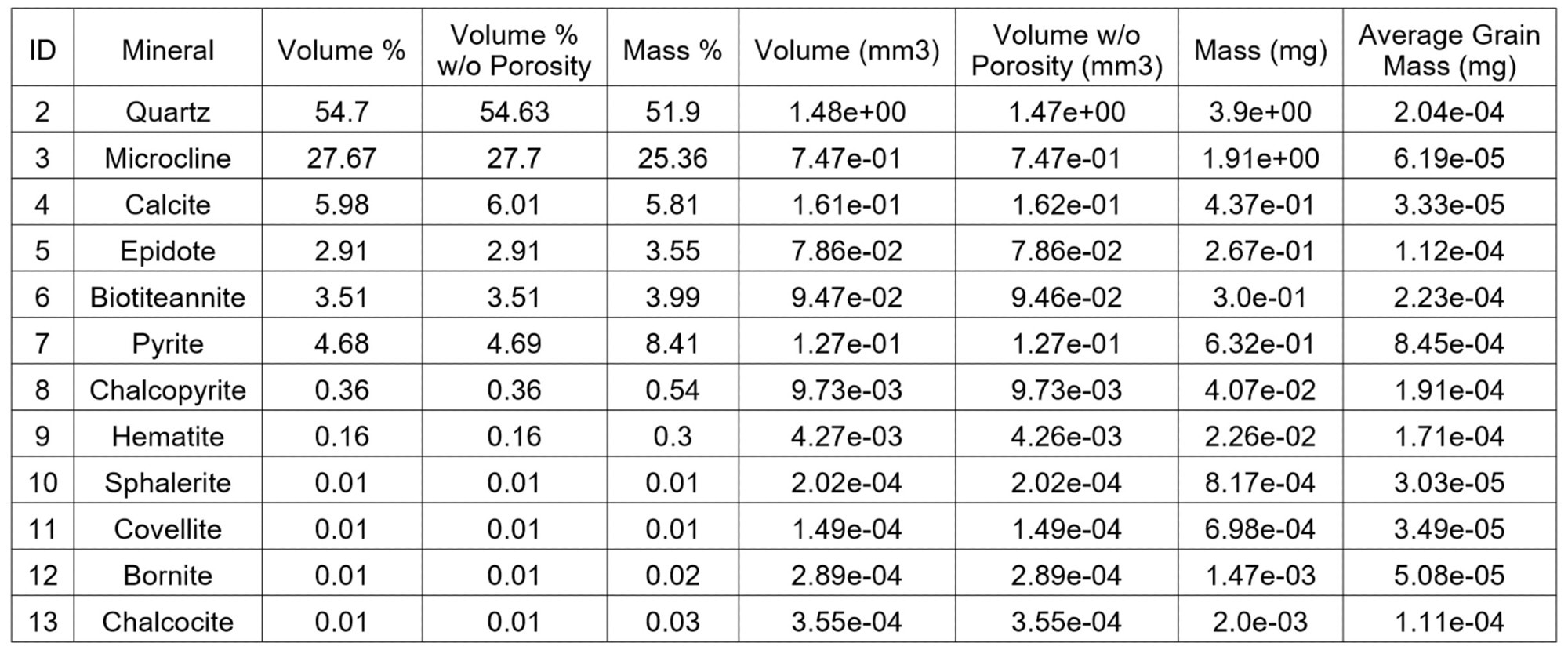
Figure 5. Modal mineralogy based on the volume of the mineralogy. Image Credit: ZEISS Raw Materials Group
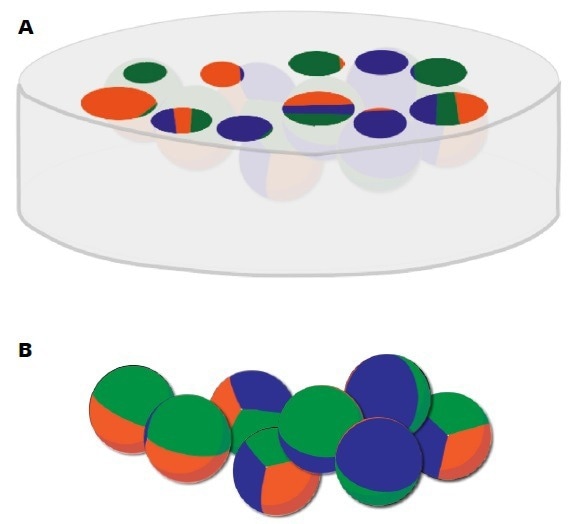
Figure 6. (A) Mechanical alteration of the sample for SEM analysis reveals fractions of particles that the user must accept as true representations of the particle. (B) With X-ray microscopy, the particle’s mineralogy and its exposure, or lack thereof, on the surface of the particle is fully recognized and measured. Image Credit: ZEISS Raw Materials Group
Liberation
Liberation is dependent purely on the proportionality of the surface exposure of a particle. For instance, a particle with a surface area of 85% chalcopyrite is already considered as liberated for chalcopyrite.
There are no surprises hidden beneath the surface as the entirety of the particle surface, and interior mineralogy, is visible, classified, and measured. This produces liberated classifications that have no intrinsic assumptions, and locked classifications for mineralogies within the particle.
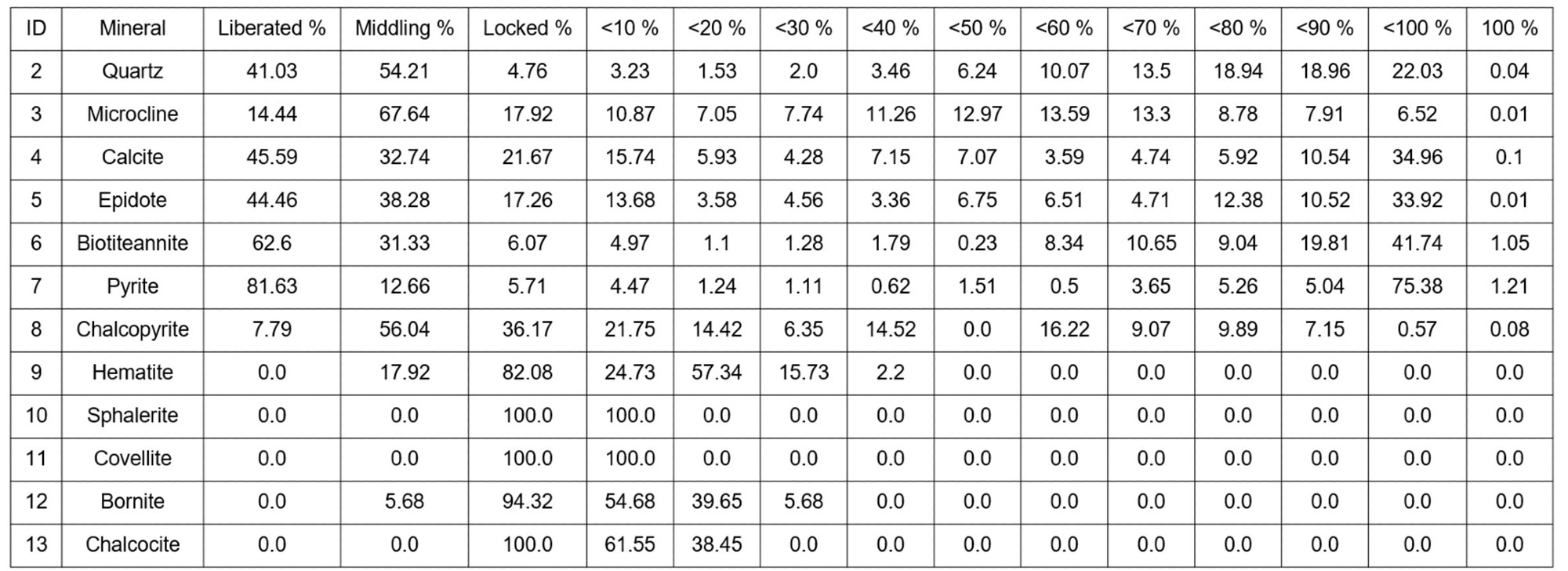
Figure 7. Liberation based on the mineral’s exposure on the surface of the particle and weighed by volume. Image Credit: ZEISS Raw Materials Group
Associations
In the 3D world, measurements of associations are performed relative to the contact of surfaces between minerals, as opposed to the linear contact applied in SEM analyses. Au-locked grain in the particle impacts the association measurement in a way that 2D techniques are not able to measure.
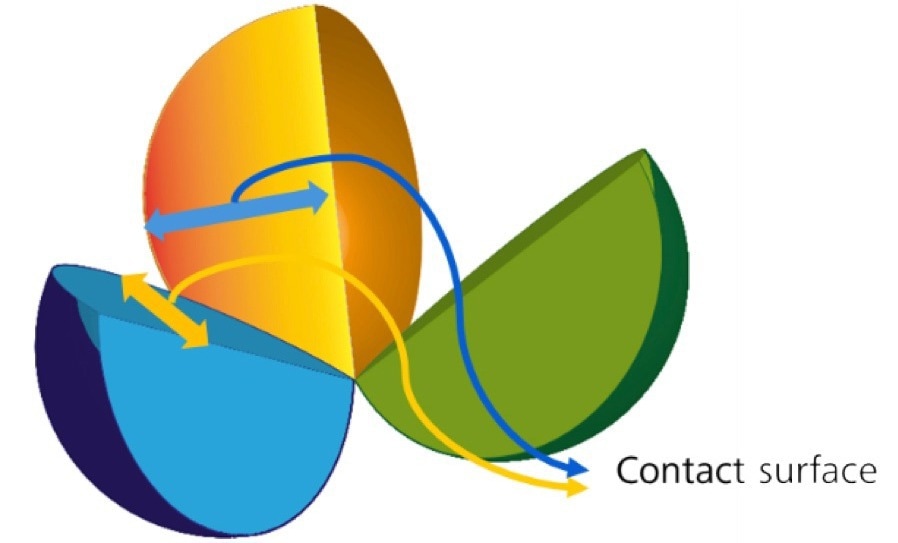
Figure 8. Particle split open to reveal the contact surfaces between minerals. It is the proportion of the surface to the total surface of the mineral in the sample that determines the level of association between the minerals. Image Credit: ZEISS Raw Materials Group
Summary
Taking significant advantage from progressive developments in X-ray microscopy and machine learning, Mineralogic 3D marks a significant advancement in automated mineralogy. The unique capacity to study samples in 3D, with no obscured mineralogy, without stereological artifacts, and acquiring precision data for each and every particle paves the way towards a new understanding of the geometallurgical behavior of ores.
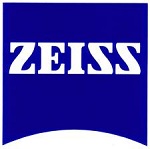
This information has been sourced, reviewed and adapted from materials provided by Carl Zeiss Microscopy GmbH.
For more information on this source, please visit Carl Zeiss Microscopy GmbH.