In this interview, Dr. Uwe König, the Global Mining Segment Manager at Malvern Panalytical, talks to AZoMining about the importance of technology and sustainability in mining.
How does your work relate to the mining industry?
I am a geologist responsible for overseeing the mining and metal segment at Malvern Panalytical.
My primary role is to innovate and create new solutions that will be essential to mining operations over the next five years. We are focusing on enhancing efficiency while aiming for carbon neutrality and waste reduction. Looking at the future requirements of the mining industry is an aspect of my job that I particularly enjoy.
Why is mining so vital to humanity?
Look around you for a moment and you will see that everything is connected to mining. Our everyday lives would be impossible without metals or minerals. These resources are essential everywhere. The prime example is iron ore; all the steel in our surroundings and buildings requires the mining of iron ore.
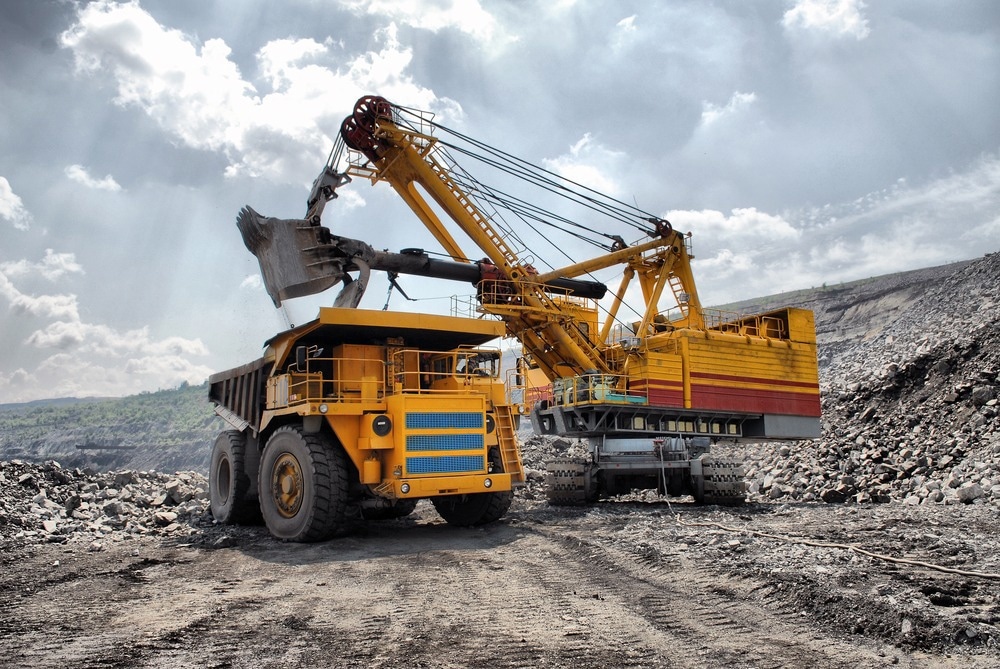
Image Credit: kaband/Shutterstock.com
Transportation, including cars and airplanes, relies on aluminum, which also needs to be mined, along with various other metals. Nowadays, even the bus route here involves 'green metals' used in batteries, such as lithium, nickel, or rare earth elements (REE) for smartphones, as well as copper for wind turbines. While recycling plays a role, it will never be sufficient to meet demand. This is why mining is so crucial to humanity.
How has mining changed over the last 100 years?
About a century ago, mining was considered one of the most perilous occupations. However, that has changed thanks to technology. While exploration remains crucial for discovering new deposits, it historically required a significant number of geologists. Now, advanced tools such as drones and airplanes can reach remote areas that were previously inaccessible to geologists.
Looking back at the history of mining technology, the tools initially used were rudimentary. Hammers were originally used to extract materials. Later, dynamite was used for extraction and manual labour for transportation. Today, there are enormous conveyor belts capable of analyzing the mined material in real time.
A hundred years ago, there were hardly any women in the mining industry. This has also changed considerably, although it is not an even fifty-fifty split yet. However, there is a much higher percentage of women in the mining industry today. Major mining companies are aiming to achieve that fifty-fifty balance in the short term.

Image Credit: Mark Agnor/Shutterstock.com
Speaking of technology, various sensors can analyze materials in ways that were unthinkable in the past – relying mainly on wet chemistry. Today, we have elemental analyzers, such as X-ray fluorescence (XRF), in addition to newer technologies. Mineralogy, once an overlooked aspect in process control, has become standard practice. Geometallurgy, a fusion of geology and metallurgy, is reshaping the mining industry.
The significant shift toward automation, not just in mines but also in laboratories, is also important. Although the mining industry tends to be conservative, it is now embracing the digital revolution. Predictive technology is helping us to explore deposits, determine precise processes, and estimate metal recovery rates.
How has modern technology driven these changes in recent years?
Unlike 50 years ago, we are not talking about one sensor or one technology anymore. The technologies are now more diversified, focusing on both speed and accuracy – which have evolved significantly. It no longer takes us hours to analyze a sample. Now it is a matter of minutes or even real-time assessment. There are solutions capable of analyzing materials as they move along the conveyor belt, determining the presence or absence of the desired metal for extraction.
In addition, automation and digitalization are trends that have progressed faster than most people anticipated. There are already fully autonomous mines where no personnel are present. Trucks operate without human drivers as if by magic, transporting materials directly onto the conveyor belt (which extends 20 kilometers from the mine for processing). This is all achieved without human intervention.
When did Malvern Panalytical become involved in mining?
I am not sure if you are aware of the history of Malvern Panalytical. Before Panalytical, it was known as Philips Analytical. In 1919, Philips brought the first X-ray tube to the market and in 1945, the first X-ray diffractometer was developed, forming the basis for the founding of the X-ray analysis group within Philips. One of our first important clients was the mining industry, which required a rapid method to analyze the chemistry and elemental composition of rocks and ores to be mined. The alternative, wet chemistry, is time-consuming and involves the use of unsafe chemicals.
How do clients use Malvern Panalytical products in mining operations?
We provide equipment that can be taken into the field, in a car or in a backpack, allowing direct analysis on-site. This helps geologists to maintain a more objective approach. When I was a student, sometimes we were sent into the field with only a color chart. We had to make decisions based solely on color, which could lead to subjective interpretations.
Nowadays, we use equipment that can be easily transported to the field. It enables us to make an immediate assessment, distinguishing between ore and non-ore materials. However, our main clients, and thus equipment too, are situated in laboratories, which is the core of our business.
We are currently seeing an increasing trend toward automation. Sample preparation and entry, once manual tasks, are now automated. We also have equipment that is used directly in the mines. For instance, there are analyzers installed on conveyor belts that allow real-time analysis.
Regarding mining operations, we also have process-integrated equipment that allows real-time analysis of process liquors. Another notable trend we have noticed is the installation of equipment in underground containers. Placing equipment in containers makes it easier to move it. You can essentially transfer an entire laboratory from one site to another.
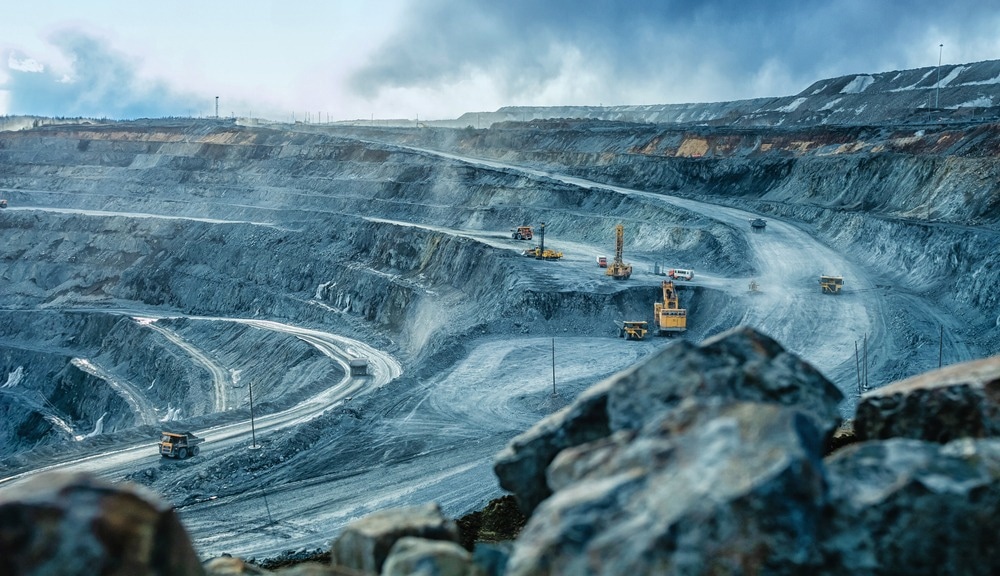
Image Credit: Evgeny_V/Shutterstock.com
What are some of Malvern Panalytical’s most significant mining products?
Traditionally, analysis in mining has focused on chemistry – that is, the elements rather than the minerals. This is why a significant part of the mining industry relies on X-ray fluorescence (XRF) – it is the largest segment of the field.
There have also been notable advances in conveyor belt solutions, such as cross-belt analyzers. However, there is a noticeable trend towards the use of different sensors. Recently, there has been a shift towards monitoring mineralogy (which involves X-ray diffraction (XRD)) and examining morphology (including particle size and shape).
This aspect combined with digitalization is very important in processing and is likely to be where we see the most growth in the future.
What major differences will clients notice between Malvern Panalytical products and those of its competitors?
I believe we are the only analytical company that covers the entire mining value chain. From the exploration tools that are taken into the field to cross-belt analyzers, the laboratories, and the environmental impact analysis methods, we have the full range covered. This sets us apart from other companies.
In addition, our extensive experience in mining means that we have a large number of experts who understand our products and can provide expertise on their practical application, equipment utilization, and ways to enhance processes.
Since the company split into different sectors, we have been actively strengthening our mining segment. This segment houses experts with domain knowledge and an application laboratory for our products. They all have extensive background in mining, which allows them to truly understand the industry and its needs.
How have environmental concerns changed mining?
Environmental, social, and governance (ESG) has been a major focus in the mining industry for several years. It is not just about ensuring people's safety but also about preserving the environment to make it more sustainable. One major impact on mining is the lengthy environmental approval cycles now required for new mines.
Obtaining the necessary permits can take a considerable amount of time, sometimes up to five or even ten years. In addition, stakeholders are scrutinizing these processes, and investors are increasingly selective about where they put their money.
Complying with ESG regulations presents mining companies with a plethora of requirements, particularly when it comes to restoring nature. Currently, there are strict regulations governing anything that is returned to the environment, such as wastewater and tailings. Consequently, mining companies must adhere to strict guidelines.
In the coming years, mines must strive to become not only carbon neutral but also waste neutral, aiming for zero waste and zero carbon emissions. The goal is to recycle as much of the waste as possible or repurpose it.
Environmental concerns currently hold significant weight. Moreover, the mining industry has historically had a somewhat negative reputation. The industry is actively working to change this perception, and the strict rules are a step in the right direction toward achieving sustainability.
How does Malvern Panalytical help clients meet environmental regulations?
We offer specialized solutions for field or in-process testing, as well as for waste or tailings reprocessing. For example, we have a solution that effectively controls the elemental composition of mine wastewater or process liquors.
About three to four years ago, there were dam collapses in Brazil that resulted in, among other things, the loss of about 200 lives. While I am not suggesting that our solutions can prevent such events, we do have tools capable of analyzing clay content. The clay content determines the stability or slipperiness of tailings.
What does the future hold for mining, and what challenges lie ahead?
Several factors are contributing to changes in mining practices. One factor arises from geological shifts; in the past, there were high-grade ore deposits that were easily accessible without extensive underground excavation. However, these high-grade deposits have become scarce worldwide, compelling mining companies to look for new, lower-grade deposits.
These lower-grade deposits require more extensive processing and are often situated in remote areas, such as deserts, rainforests, or beneath the Greenland ice sheet. Investigations into submarine deposits are underway, but their acceptance within the community is contentious due to environmental concerns.
I prefer to explore desert regions rather than submarine locations due to the harsh nature of underwater life. The evolution of mining technology is evident, transitioning toward smart mines controlled by sensors, drones, and advanced technology – a shift that is already underway.
Environmental sustainability is a crucial aspect; mining companies must strive for carbon neutrality and waste neutrality – a goal that is yet to be fully achieved. The concept of a circular economy, where extracted resources are recycled or reintegrated, is gaining traction.
Collaboration between mining companies and equipment suppliers, along with analytical expertise, is key to addressing these challenges. The future lies in collective problem-solving, where specialists in mining, analytics, and other related fields work together to promote sustainability and innovative approaches.
How will Malvern Panalytical help its clients meet and overcome these challenges?
For several years now, we have had a dedicated group handling automation. They usually accompany me to mining companies to discuss the client’s specific problems. If there is a need for automation, we customize solutions for each mine. As there is no standard automation solution, our new digital group comes into play.
This group is meeting the industry's demands by delving into machine learning and artificial intelligence, using both our sensors and those of our customers.
About Dr. Uwe König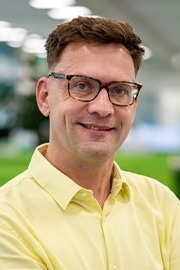
Dr. Uwe König studied mineralogy and geology at the Martin-Luther-University Halle (Germany), with a master thesis on the quantification of iron ores using X-ray diffraction and the Rietveld method and a PhD thesis on synthesis and characterization of manganeous layered double hydroxides (LDHs). In 2005 Uwe joined the company as an application and product specialist . His focus is the development of new XRD applications for the mining, minerals and metals industry.
About Malvern Panalytical
Malvern Panalytical technologies are used by scientists and engineers in a wide range of industries and organizations to solve the challenges associated with maximizing productivity, developing better quality products and getting them to market faster. Our mission is to create superior, customer-focused solutions and services to deliver tangible economic impact through chemical, physical and structural analysis of materials.
Malvern Panalytical was formed by the merger of Malvern Instruments (Malvern, UK) and PANalytical, including ASD and Claisse (Almelo, the Netherlands) on 1st January 2017, and employs over 2,000 people worldwide. With R&D and manufacturing sites in North America, Europe and China, and a global sales and service presence, Malvern Panalytical provides unrivalled levels of customer support. Malvern Panalytical is a leader in the materials characterization market, developing expert analytical solutions which deliver superior actionable insight.
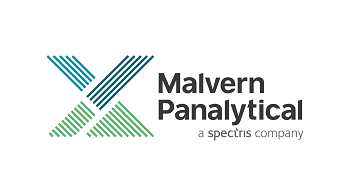
This information has been sourced, reviewed, and adapted from materials provided by Malvern Panalytical B.V.
For more information on this source, please visit Malvern Panalytical B.V.
Disclaimer: The views expressed here are those of the interviewee and do not necessarily represent the views of AZoM.com Limited (T/A) AZoNetwork, the owner and operator of this website. This disclaimer forms part of the Terms and Conditions of use of this website.