MTM Critical Metals Limited (MTM or the Company) has received results from testing of coal fly ash (CFA) samples using Flash Joule Heating (FJH). FJH processes improve the acid leachability of rare earth elements (REE) by over 50% and a range of critical metals by between 50% and 514% when compared to traditional acid leach methods.
MTM Chairman, Mr John Hannaford said: “These promising initial results from coal fly ash samples treated with flash joule heating show the value in our recent acquisition that included this industry-leading technology. This innovative approach holds the potential to transform the current methods used by the industry to recover critical metals from waste materials. We look forward to providing updates on the technology, as we scale operations to service a range of applications.”
Flash Metals USA President, Mr Steve Ragiel said: “We are thrilled with the progress of our Flash Joule Heating prototype testing, demonstrating significant increases in the extraction of rare earth elements and critical metals from coal fly ash. We have validated the Rice University results, showing the technology has the potential to dramatically increase the leaching recovery of metals from waste materials that are otherwise very difficult to treat, all while using significantly less acid. Processing of samples from additional metals remains ongoing. We look forward to continuing our testing and advancing towards commercial scale opportunities.”
Test Work Method and Results
The FJH protype unit was designed and fabricated by KnightHawk Engineering (KnightHawk) in Houston, Texas and verified in consultation with the developer of the technology, William Marsh Rice University (Rice) a prominent industrial technology research institution also based in Houston. The Prototype sample test volumes represent an approximate 50x increase in scale versus previous proof of concept testing performed by Rice.
Approximately 60 kilograms of coal fly ash (CFA) sourced from North Dakota, USA, was utilised as a basis for the current round of FJH testing. The CFA samples were tested using both a standard leach process to determine an approximate metal recovery using conventional acid leach methods, as well as treating the CFA with the FJH technology.
Preliminary results showed that the CFA treated with FJH resulted in a 50% recovery increase in REE, and importantly, a 72% increase for neodymium when compared to control samples. Several other important critical metals also showed enhanced leach recoveries, including cobalt (+73%), lithium (+50%), nickel (+99%), rubidium (+113%), scandium (+103%) and titanium (+514%). This is of particular significance given the current market price of Rubidium is $108,000/kg and the MREE element Praseodymium, is currently US$68,800/tonne.
Importantly, the CFA material treated with FJH technology shows significant promise for delivering higher recoveries in the leaching process when compared to recovery processes on the same material which has not undergone FJH processing. The ability of FJH to reduce the acid requirements in the leaching process offers both potential cost savings and for the generation of less waste. Future testing will be able to quantify both the energy and reagent savings in the leaching process.
MTM, in conjunction with KnightHawk and Rice University, will continue to test CFA samples using the data to help refine and improve the technology with the aim of increasing recovery rates. The technical and performance data from these tests will provide valuable information for MTM to advance the design of a larger Pilot FJH Plant.
MTM will also look to commence testing of the FJH technology on other waste sources of REE and critical metals including bauxite residue (red mud), e-waste and end of life lithium-ion batteries. The initial results from the prototype testing, coupled with the strong pricing dynamics of the metals recovered from the CFA material, highlight the economic potential of FJH.
Flash Joule Heating
FJH is an advanced processing and recycling technology being developed to extract critical metals including REE, titanium, nickel, cobalt and lithium from waste material including lithium-ion batteries, e-waste, coal fly ash produced by coal-fired power stations or bauxite residue derived from alumina refining.
The FJH technology is an electro-chemical process that involves the rapid and intense heating of material to both directly recover critical metals and make materials more amenable to metal recovery through conventional acid leaching methods. The FJH technology that is being licensed to MTM uses proprietary intellectual property in the flash process enabling the extraction of various metals including REE’s, Lithium and other valuable precious and industrial metals. The FJH technology incorporates a range of patent protected processes around the material preparation, energy application and vaporized component separation and collection which can be scaled due to the precise control that the FJH prototype module provides.
MTM has secured the option over the FJH technology via the recent acquisition of Flash Metals Pty Ltd and the Company is currently finalising a global licencing agreement with Rice.
Table 1: Selected CFA leaching results showing the positive effect on metal recovery using FJH technology.
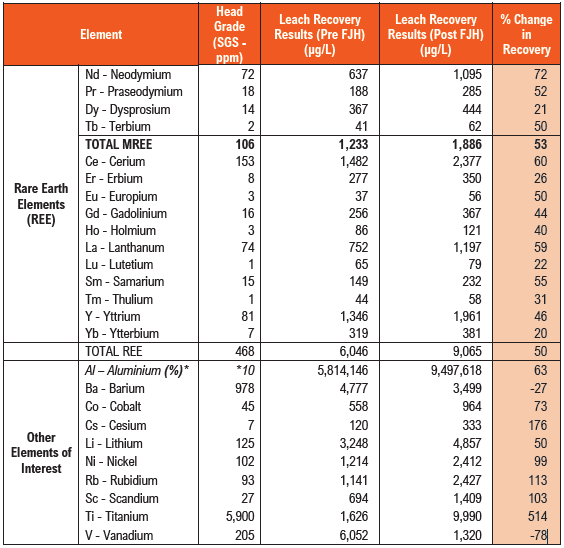
Notes:
- Results are preliminary and un-optimised.
- Head Grade composition of CFA measured by SGS on a component specific basis (Note Appendix I).
- * Aluminium is reported in percentage due to the high amount of Aluminium content within the CFA sample for SGS values.
- Appropriate rounding has been applied to the reported values.
- The “Leach Recovery Results (Pre FJH)” and “Leach Recovery Results (post FJH)” data were measured using the KnightHawk standard Acid Leaching procedure (Appendix II) and the PerkinElmer TotalQuant semi-quantitative ICP-MS procedure (Appendix III) and are typically within ±30% of the quantitative values.
- In the coming weeks, KnightHawk Engineering expects to have more quantitative results utilising detailed calibration curves for ICP-MS data refinement.
- MREE – Magnetic Rare Earth Elements.