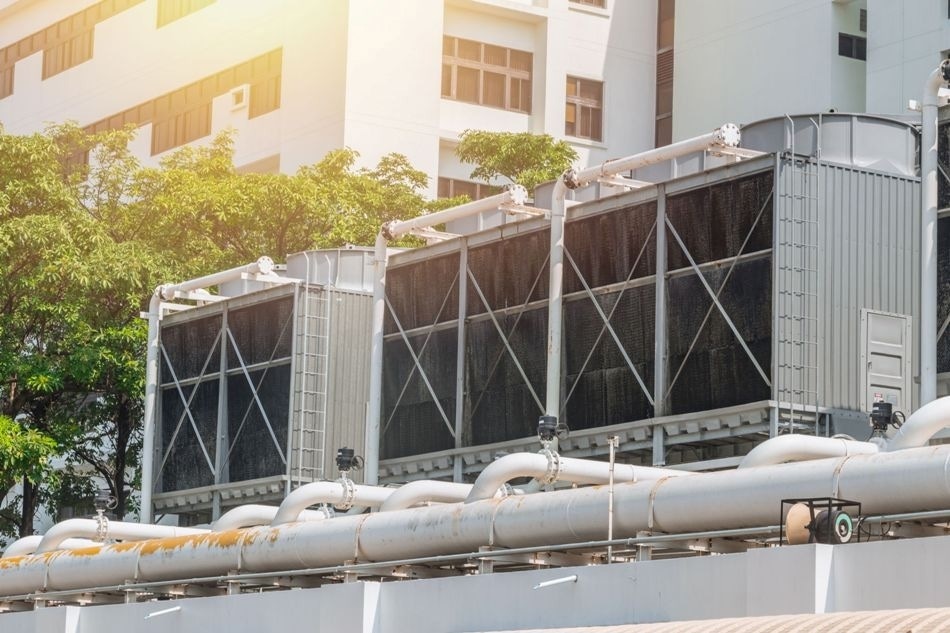
Chillers find applications across various industries to eliminate heat from facilities or from processes. A few examples include chemical processes that need a consistent supply of chilled water for their processes or commercial brewing processes that maintain their whole brew houses close to zero degrees Celsius.
In general, chillers work either by vapor compression or by the absorption/refrigeration cycle. At present, the absorption/refrigeration cycle is not extensively used in industry and therefore, focus is given to chillers that work based on the vapor compression technique. In this technique the refrigerant liquid absorbs heat, causing it to boil and convert from the liquid to the gas phase. As the heat is removed from the process, the gas is subsequently compressed back into a liquid.
Ask the Expert: Chiller Oil Analysis
Just like a home air conditioner, the heat which is removed is usually outside of the facility, and hence there is a net heat transfer from the medium being chilled to the surrounding.
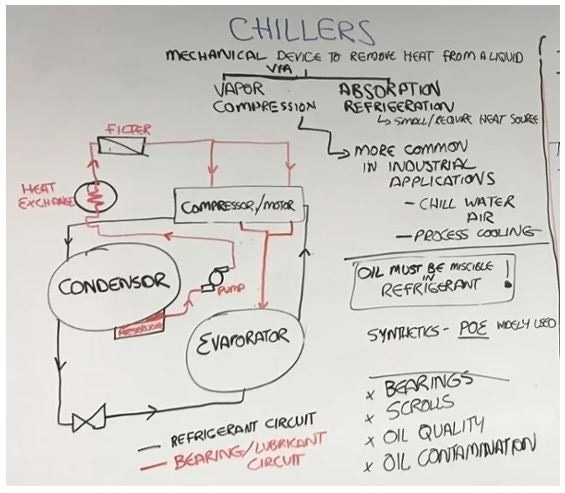
As these systems are usually sealed, the refrigerant can't escape. As a consequence, it's reasonable to ask why does one need oil analysis on a sealed system? The brief answer is yes. The liquids present in these systems still have to be moved around and compressed by scrolls and pumps. What one needs to observe is the condition of the bearings as well as other moving parts in the components driving these systems. One particular interest is to monitor the scrolls, the bearings, oil contamination, and oil quality.
A specific thing regarding compressors is that the lubricant must be able to mix with the refrigerant that drives the system. The manufacturer will usually suggest lubricating oils that are well-suited for its units and selected refrigerants. Modern ozone-friendly refrigerants usually need synthetic oils. Polyol ester lubricants have become relatively common in chiller systems.
Why Monitor?
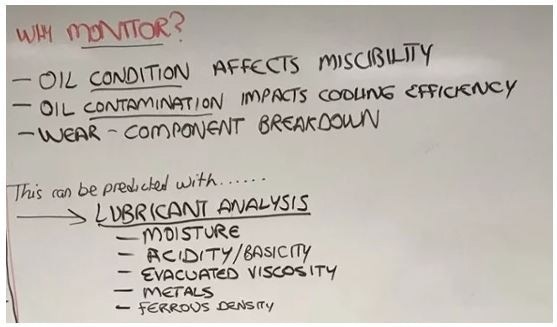
Oil Condition
Oil condition can influence the miscibility of the lubricant in the oil. One should examine oil to ensure that it is the exact type of oil required and is in good condition
Oil Contamination
Oil contamination can have a negative impact on the chiller efficiency. Particularly, water contamination can decrease the chiller efficiency.
Wear
As stated before, the scrolls and the bearings are the main components to be monitored. Bearing failure is indicated by excessive contamination or wear debris. Early detection enables one to make repairs before the system breaks down. Early intervention is usually less costly and eliminates expensive downtime.
What Specific Tests do Users Care About?
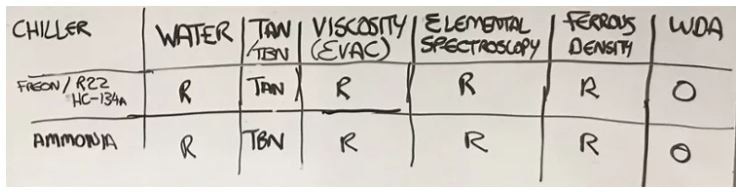
Moisture
Water contamination will not only reduce the efficiency of the chiller, but will also lead to freezing and corrosion problems. Ensuring the dryness of the oil can save users a lot of problems in the future.
Acidity/Basicity
In the case of chlorinated refrigerants like R-22 or Freon, it is advised to run a Total Acid Number (TAN) test. For ammonia-based systems, it is advised to run a Total Base Number (TBN) test. The miscibility of the lubricant in the refrigerant is influenced by TAN.
Evacuated Viscosity (40 °C)
The resistance of a liquid to flow under the force of gravity is referred to as kinematic viscosity. It is the most significant physical characteristic of a lubricant. If the viscosity is off in a chiller system, it is indicative that the separator is not functioning properly.
Sometimes, viscosity measurement in chiller systems can be challenging, as the refrigerant dissolves in the lubricant and must be outgassed frequently before achieving an accurate viscosity measurement. This can involve several hours. However, this is not needed if the Spectro Scientific MiniVisc 3000 is used. The MiniVisc’s split capillary design permits lubricants to outgas while the measurement is being made.
Metals
Elemental analysis of metals can establish the cause of any contamination enabling users to more easily detect the cause of the problem
Ferrous Density
A severe increase in ferrous wear or the size of ferrous particles usually indicates that an abnormal wear condition is becoming worse. Monitoring of ferrous particles requires the intervention of maintenance staff before a failure becomes disastrous.

This information has been sourced, reviewed and adapted from materials provided by AMETEK Spectro Scientific.
For more information on this source, please visit AMETEK Spectro Scientific.