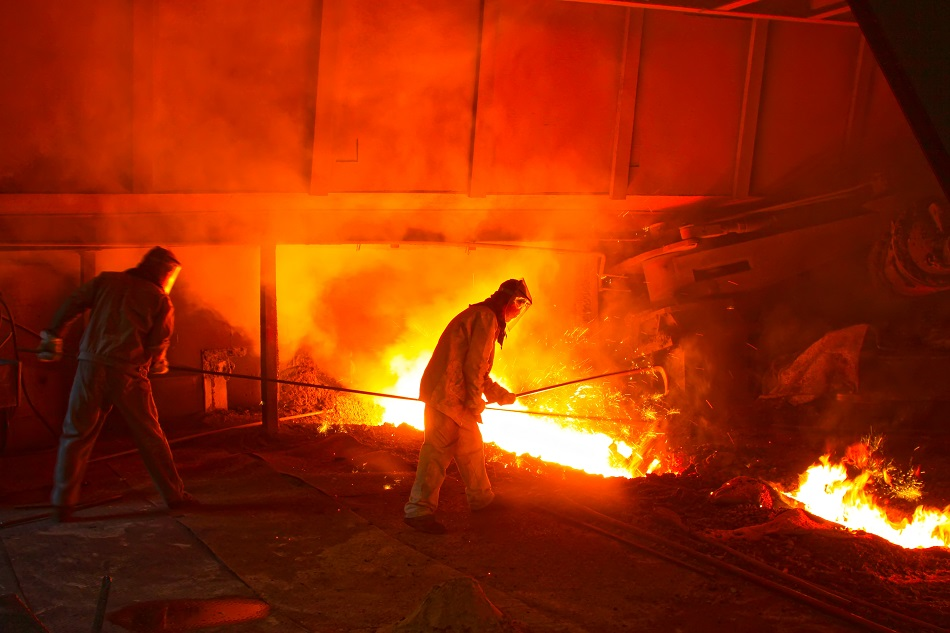
Image Credit: junrong/Shutterstock.com
The mining industry is one of the most energy-intensive sectors in the world. Ore, once extracted, needs to be processed into useable materials which can then be turned into a multitude of products for industries including construction and engineering.
Furnaces are common in the mining industry and have been used since ancient times. From crude, prehistoric affairs to ultra-modern industrial equipment, the furnace has undergone several technological evolutions over the millennia, and along the way mining processes have been steadily improved. The need for high-quality ore processing has necessitated this.
Bloomery Furnaces
Bloomery furnaces were one of the earliest types of furnace capable of smelting iron. Iron, a material that is found everywhere in the modern world from buildings to electronics, provided the human race with one of the most important technological revolutions in history. Bloomery furnaces worked by producing a bloom - a porous mass of iron and slag. This sponge iron could then be worked into wrought iron.
Bloomery furnaces consisted of a heat-resistant chimney (made of materials such as clay, stone, or earth) and pipes called truyeres which allowed air to enter into the furnace. Air would either enter via natural draught, or a bellows could be used. The resulting bloom would either be removed through an opening at the bottom of the entire furnace could be dismantled to remove it.
A version of the bloomery furnace that survived into the 19th century was the Catalan Forge in Spain.
Blast Furnaces
Blast furnaces have largely superseded bloomery furnaces. These single-chamber furnaces produce pig iron, which has a higher iron content than the bloom created by the bloomery furnace. Blast furnaces can also be used to smelt other metals including lead and copper.
Ore, coke, and limestone are fed into the top of the furnace and preheated air is blown into the bottom. Raw materials descend through the blast furnace over the space of several hours, with the end product being liquid slag and ore. This is then removed at regular intervals, and a blast furnace can operate for several years, only being turned off for the purposes of maintenance. Some modern blast furnaces are large constructions that can process tons of ore and metal.
Mechanical Furnaces
There are several different types of mechanical furnace which are used in the mining industry worldwide. Reverbatory furnaces isolate the material from coming into contact with the fuel, but not the combustion gases. Reverbatory furnaces have disadvantages in efficiency compared to blast furnaces, however, both radiant heat and convection need to be utilized effectively to maximize heat transfer, whereas blast furnaces do not need this. They have been in use since the medieval period.
Broadly, there are four classes of mechanical furnaces:
- Stationary hearth furnaces – Moveable iron hoes “rabble” the ore.
- Rotating-bed furnaces – The hoes are stationary, but the ore bed moves.
- Rotating cylindrical furnaces – Brick-lined cylinders rotate, tumbling the ore whilst it is being roasted.
- Shaft furnaces – Powdered ore falls via gravity in an ascending column of hot air. Oxidation is carried out during the fall. The Stetelfeldt furnace is an example, which was widely used for the smelting of silver ore in the western United States.
Mechanical furnaces have several variations that have been used throughout the 19th and 20th centuries. The O’Hara furnace is the oldest mechanical furnace variant. This furnace is closest to the reverbatory furnace, with two superimposed hearths where the heat is confined close to the ore. Iron plows or hoes, attached to a chain at intervals, turn the ore to the center and move it to the walls, thoroughly stirring the ore.
Other notable examples are the Spence furnace, which has four or five superimposed hearths which communicate via vertical passages and rabbles the ore with reciprocating rakes, and the Pearce Turret Furnace, which operates via rakes attached to a rotating column.
Mechanical furnaces represented a technological leap forward in the mining industry as there were savings on manpower through increased automation, which conferred economic savings and improved efficiency.
Induction Furnaces
However, there are several problems with traditional mechanical furnaces. They can be quite energy-intensive, requiring large amounts of fuel to operate, and can produce unwanted products including smoke, dust, and pollutants, which is undesirable in the modern era.
Induction furnaces are modern electric furnaces that do not have these problems. These furnaces utilize induction coils to heat the ore, have an electric power supply, and are water-cooled. Induction furnaces are highly efficient, needing no fuel whatsoever to melt the desired substance, which is advantageous for the modern mining industry.
Sources and Further Reading
Disclaimer: The views expressed here are those of the author expressed in their private capacity and do not necessarily represent the views of AZoM.com Limited T/A AZoNetwork the owner and operator of this website. This disclaimer forms part of the Terms and conditions of use of this website.