Applications of high-precision laser scanning technologies have increased in the mining industry in recent years. This article will look at SKALA 3D’s automated mobile laser scanning technology for surveying mine shafts, a critical element of mining infrastructure.
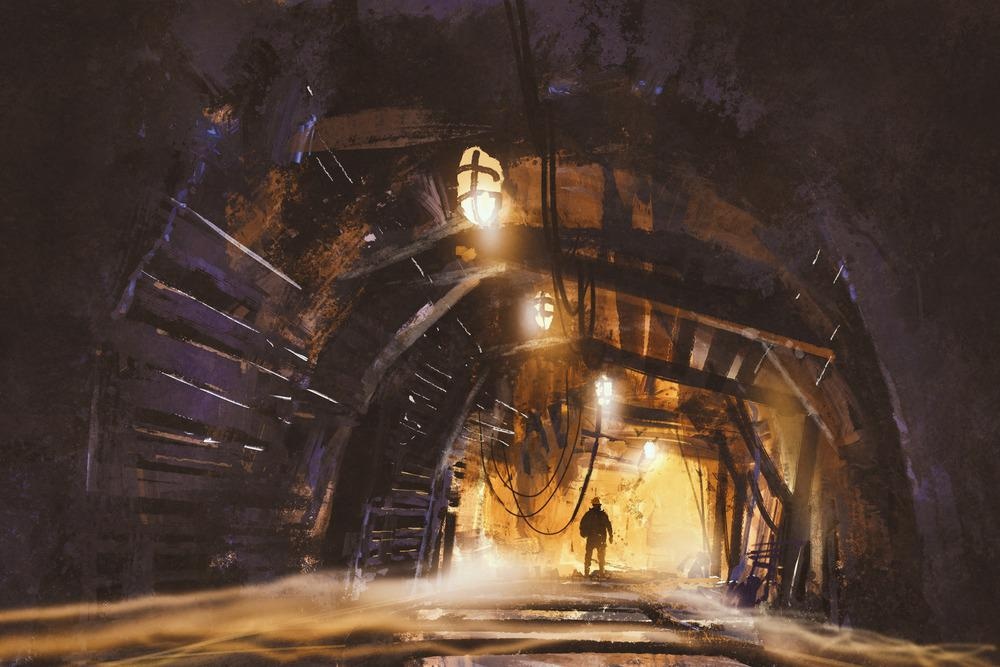
Image Credit: Tithi Luadthong/Shutterstock.com
The Importance of Mapping Mine Shafts
Mine shafts are vital to the design and safe operation of mines. These infrastructure elements are governed by a specific set of rules, can be difficult to access, and are known for having unfavorable conditions for mapping and measurements. Regular surveys and inspections need to be carried out on them to ensure proper operation and identify any structural and safety issues.
Mine shafts serve multiple purposes: they are used to transport workers and goods, provide vital ventilation for people working in the mine, and are used for resource extraction. If regular mineshaft mapping is not carried out, the risk of catastrophic failure increases. This can lead to loss of life and equipment and increased costs to the mine operator.
Laser Scanning in the Mining Industry
Mapping mine shafts relies on measuring the geometry of reinforcements and linings, measuring the conveyance track’s rectilinearity, and measuring the play between guides and working surfaces of shaft slides.
Laser scanning has increased in use in the mining industry thanks to the development of innovative technologies and the recognition of key challenges in mining. Current technologies include high-precision panoramic scanners, handheld, and backpack scanners which are based on SLAM algorithms.
The use of laser scanning to map mine shafts has been increasing, but challenges exist with widespread implementation. This is due to the characteristics of the mine shaft and the lack of satellite coverage. Mobile automated laser scanning equipment must overcome these challenges.
MSS, SKALA 3D’s Mineshaft Mapping Technology
Automated mobile laser scanning has significant advantages over other surveying methods. It is more accurate, improves worker safety, and minimizes costs. Inspection time is reduced by as much as 50-70% compared to other technologies. Depending on the scope of the work needed, inspections can be carried out in the span of 8-16 hours, or 1-2 shifts. Operator involvement is reduced to observation and plumb lining, if necessary. Operations are carried out inside the safety of the cage.
The Mining Survey System (MSS) is SKALA 3D’s new solution for automated laser scanning and mapping of complex mineshafts. The MSS has many advantages over conventional laser scanning applications currently in use in mining operations to map shafts.
The methodology developed by SKALA 3D to calculate the accurate trajectory and reconstruct an accurate three-dimensional map of the mineshaft includes initial trajectory estimation, calculation of relative position and orientation between consecutive trajectories, refinement of final trajectories, and refining trajectories by fusing them with fully georeferenced data.
This fully automated mobile laser scanning equipment uses terrestrial laser scanning technology and internal positioning support systems. MSS makes it possible to create spatial models of objects with a 1-3 mm accuracy. In-built vibro-isolator systems compensate for vibrations from the moving cage that houses the scanning equipment and operators. The system can also operate in areas with limited or no GPS coverage. The system can supply complete spatial data within hours.
The system has several measurement characteristics, including the measurement of 1 million+ points per second from all lasers, 450Hz IMU readings, and a total ride time in a vertical shaft of 1.5-2 hours plus additional set up time and further related activities.
Profilers and imagers provide a point cloud profile every 2.5 mm. The cage containing the scanning equipment moves between 0.1 and 12 m/s. The impact on the algorithm is minimal due to a panoramic Lidar setup. The optimal speed is 1 m/s.
Control and post-processing of data are handled by an onboard software suite. The system uses components that can be found in other applications, but on a global scale, it is unique. Automation of the entire process significantly improves operator safety due to minimal intervention needs.
Key Challenges of Mobile Laser Scanning Systems
Three key hardware challenges have been addressed in the design of the MSS automated mobile laser scanning system: Automation, increasing mine surveyor safety and reducing inspection time to decrease overall costs. Inspection is faster and safer with the MSS system than classical methods.
Aside from hardware challenges, challenges in data acquisition have been addressed by SKALA 3D. The large amounts of data call for a large computational power in laser scanning systems. Overall performance is improved via the parallel processing of orthogonal computational subproblems. The software challenges require significant investment in hardware and software to achieve reliable and efficient alignment and processing. However, MSS remains the best technology for accurate scanning of mineshafts.
The Future of Mine Shaft Mapping
MSS from SKALA 3D is a state-of-the-art innovative solution for the mining industry. Despite some key challenges, it represents the next step in safe, efficient, and accurate mineshaft scanning. Data gathered by mineshaft mapping surveys using this equipment will inform the upkeep of mineshafts and the overall safe operation of mining infrastructure and operations.
References and Further Reading
Adamek, A & Będkowski, J (2021) Automated Mobile System for Mapping Mineshafts [online] gim-international.com | GIM international. Available at: https://www.gim-international.com/content/article/automated-mobile-system-for-mapping-mine-shafts
SKALA 3D (2021) Mining Survey System (MSS) [online] skal3d.pl | Skala 3D. Available at: http://skala3d.pl/en/technologies/mobile-systems/mining-survey-system-mss/
Disclaimer: The views expressed here are those of the author expressed in their private capacity and do not necessarily represent the views of AZoM.com Limited T/A AZoNetwork the owner and operator of this website. This disclaimer forms part of the Terms and conditions of use of this website.