Deep-sea mining pumps are a vital part of deep-sea mining infrastructure. Pumps are subjected to wear from coarse-grained minerals, leading to increased upkeep costs and interrupted operations. Particle flow analysis can be utilized to study the characteristics of flow passage components, providing relevant information for optimal pump operations. This article will discuss the application of particle flow analysis for this vital mining purpose.
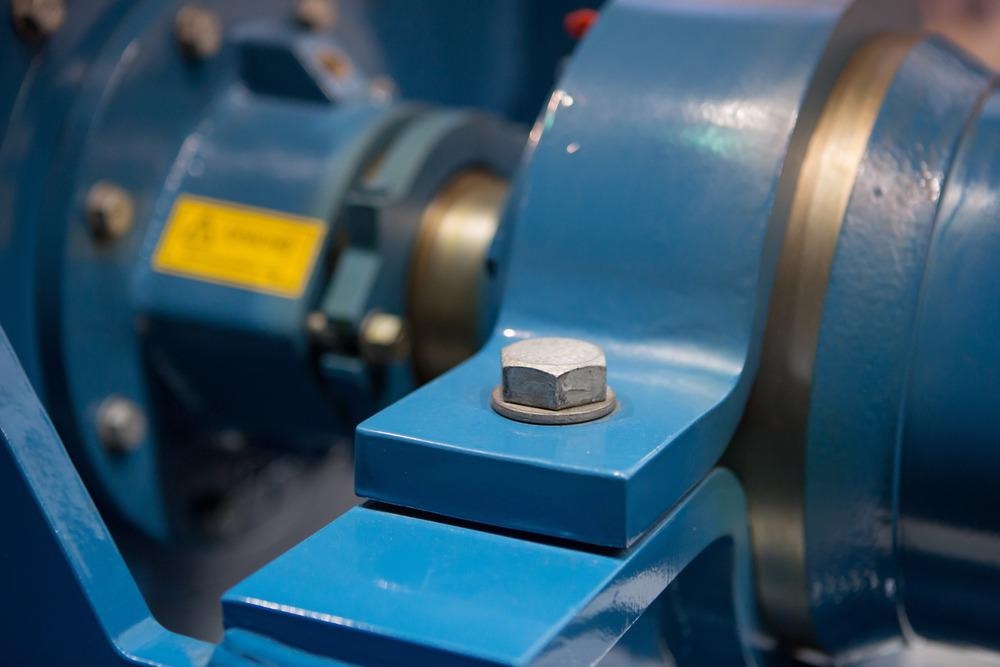
Image Credit: krigo/Shutterstock.com
Deep-Sea Mining
Due to the depletion of land-based resources, attention has shifted to retrieving mineral resources from the ocean floor. The current focus in the deep-sea mining industry is the development of efficient machinery that can extract resources from these hard-to-reach areas.
The most promising deep-sea mining solution is the pipeline lifting system. Resources are collected by a mining vehicle on the ocean floor and travel through a pipe to the midtransferring buffer. Here, they undergo remixing of the volume concentration of ore, before being pumped through the pipeline lifting system by the slurry pump to the surface vehicle.
The only working part of the system is the slurry pump. Due to its complicated structure, it can easily become clogged by high localized concentrations of ore resources and slurry if it is not maintained properly. The slurry contains a complex mixture of both ore resources and commercially useless inorganic and organic particles.
The Importance of Monitoring Slurry Pumps and Understanding Particle Flow
If slurry pumps get blocked, they can break down, severely impacting ore mining operations. Lost time, increased costs, equipment and resource loss, and worker safety can all be affected by a blocked or broken slurry pump. The efficiency and reliability of the pump are central to the entire process. Therefore, it is vital that equipment is regularly checked for problems.
Several international studies have been performed over the past few decades into optimizing the design of slurry pumps. Pumps developed by several companies have all encountered problems with wear, local particle blockage, and backflow blockage. Both laboratory tests and sea trials have demonstrated challenges with the technology that hampers its commercial viability.
In essence, all designs inevitably have serious problems with insufficient overcurrent capacity, blockage, and wear. These problems are directly related to the complex nature of ore resources and slurries, the flow pattern of particles groups, temporal and spatial distribution of particles, and their dynamic migration. Moreover, it is important to study non-steady-state wear characteristics of electrical pump over-current components as these are integral to the design, optimization, testing, and operation of slurry pumps.
To overcome engineering problems with slurry pumps, the laws and mechanisms of particle-water flow within the pumps must be fully understood. Moreover, particle diameter is an important parameter as it is central to determining the size of particles suitable for pump pipe transportation. This is related to the cost of crushing and recovering ore and the overall energy consumption of the system. However, these dynamics and parameters are still poorly understood.
Current Research
Many factors influence the wear on pump materials by particles. There have been numerous studies that have investigated these factors, aiming to improve deep-sea mining pump design. A selection of current research in this area is listed below.
Song et al. analyzed double-suction centrifugal pumps and the wear on them caused by particles, providing a reference for predicting wear. Liu et al. has established a relationship between particle shape and wear rate, analyzed wear mechanisms, and studied how particle size affects material wear, experimentally verifying their observations. The wear mechanisms of different particles colliding with materials at varying angles was studied by Takaffoli et al.
Peng et al. has optimized the design of a centrifugal slurry pump impeller by analyzing wear characteristics of particle flow based on an Euler-Euler mixture model, comparing the wear of the original and the optimized pump. Results of Nyugen et al’s study on the wear induced by different sand particle sizes demonstrated that as the particle size increases, there is a change in the wear profile from a W shape to a U shape.
Wang et al. has demonstrated that the power of both the shaft and the pump head decreases as particle size and sludge concentration increase. Moreover, several researchers have studied movement characteristics of particles in pumps from differing points of view whilst also analyzing the influence on wear and efficiency by particle size and slurry concentration.
CFD-DEM Methods
Whilst widely used in current studies, solid-liquid two-phase flow methods have limitations. They assume that the solid phase is a continuous pseudo fluid, which limits the accurate prediction of non-uniform solid characteristics. In this type of analysis, local averages are used.
A recent method proposed to overcome this issue and provide a more accurate analysis of the dynamics of solid-phase flow is the CFD-DEM method. This method is applied to study the coupled flow between continuous and solid phases in pumps. The discrete element method (DEM) is a display solution that has the ability to directly resolve particles without making assumptions that are central to the solid-liquid two-phase analysis.
Each discrete particle’s force and motion trajectories are tracked in Lagrange coordinates, and the interaction forces between both particles and the wall of the equipment are determined by a contact-mechanics model, which is much simpler. The flow of particles as well as their collision behavior can be calculated with high accuracy. Rich information on micro-particles can be obtained using this method, even information that is difficult to measure in tests.
Summing Up
Analyzing the particle flow and behavior, which is influenced by multiple factors including particle size, spatial and temporal distribution, and particle shape, is central to designing and monitoring deep-sea mining pumps to minimize damage, financial loss, safety issues, and operational downtime.
As the mining industry seeks to exploit more undersea resources, research into the dynamic nature of particle flow and mitigating equipment damage is crucial.
References and Further Reading
Hong, S & Hu, X (2022) Study on the Non-Steady-State Wear Characteristics and Test of the Flow Passage Components of Deep-Sea Mining Pumps Applied Sciences 12(2) 782 [online] Available at: https://www.mdpi.com/2076-3417/12/2/782
Wang, R et al. (2021) Impact of Particle Sizes on Flow Characteristics of Slurry Pump for Deep-Sea Mining Shock and Vibration vo. 2021 Article ID 6684944 [online] Available at: https://www.hindawi.com/journals/sv/2021/6684944/
Ning, C et al. (2022) Numerical Analysis of Single-Particle Motion Using CFD-DEM in Varying-Curvature Elbows JMSE 10(1) 62 [online] Available at: https://www.mdpi.com/2077-1312/10/1/62
Song, X et al. (2014) Numerical Prediction of Erosion Based on the Solid-Liquid Two-Phase Flow in a Double-Suction Centrifugal Pump JMSE 9(8) 836 [online] Available at: https://www.mdpi.com/2077-1312/9/8/836
Liu, Z.G. et al. (2014) A numerical study on the effect of particle shape on the erosion of ductile materials Wear 313: 1-2 pp. 135-142 [online] Available at: https://www.sciencedirect.com/science/article/abs/pii/S0043164814000763
Takaffoli, M & Papini, M. (2012) Numerical simulation of solid particle impacts on Al6061-T6 Part II: Materials removal mechanisms for impact of multiple angular particles Wear 296: 1-2 pp. 648-655 [online] Available at: https://www.sciencedirect.com/science/article/abs/pii/S0043164812002657
Peng, W & Xuewen, C (2016) Numerical simulation of solid particle erosion in pipe bends for liquid–solid flow Powder Technology 294 pp. 266-279 [online] Available at: https://www.sciencedirect.com/science/article/abs/pii/S0032591016300717
Nguyen et al. (2016) Effect of particle size on erosion characteristics Wear 348-349 pp. 126-137 [online] Available at: https://www.sciencedirect.com/science/article/abs/pii/S0043164815005098
Disclaimer: The views expressed here are those of the author expressed in their private capacity and do not necessarily represent the views of AZoM.com Limited T/A AZoNetwork the owner and operator of this website. This disclaimer forms part of the Terms and conditions of use of this website.