Topics Covered
Overviews
Advantages of Service Agreement
Conclusion
About Atlas Copco
Overview
PT United Tractors Semen Gresik (UTSG), a joint venture between PT. Semen Gresik (Perse-ro) Tbk and PT. United Tractors Tbk, was incepted as a mine contracting company in October 15, 1992. A specialist in limestone and heavy equipment rental, UTSG is an ISO 9001 and ISO 14001 certified company has won awards as an Astra Friendly Company and Astra Green Company.
For more than a decade, UTSG has been able to keep its fleet of four Atlas Copco ROC F7 surface rigs in good condition, thanks to the service contract with Atlas Copco. A green flag flying over the cab of these rigs signals that it is in proper working condition.
Advantages of Service Agreement
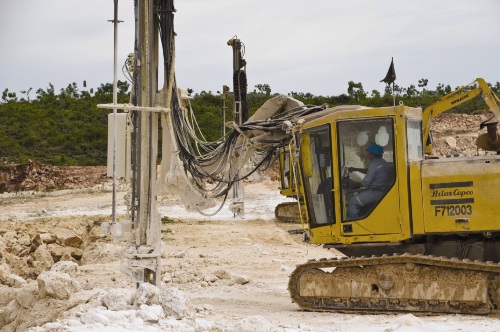
According to Sri Haryanto, Managing Supervisor for the Maintenance Department at UTSG, the company’s target is physical availability. It requires 85% availability for the transportation unit and 87.5% for heavy equipment.
Eleven years ago, UTSG made the decision to contract maintenance work to drill specialists at Atlas Copco. However, it continues maintenance service on its other machines such as excavation equipment and trucks.
Service Technician Slamet Nahdudin from Atlas Copco has been involved in the maintenance of the UTSG’s fleet since 1999. Nahdudin has years of preventative maintenance experience on drill rigs. His expertise is demonstrated by 90% availability for UTSG’s fleet of ROC F7 drill rigs.
Nahdudin credited the quality of the rig, saying maintenance for the most part is a matter of changing the necessary fluids whenever required and conducting audits according to schedule. This has minimized breakdowns and keeps the rigs running smoothly.
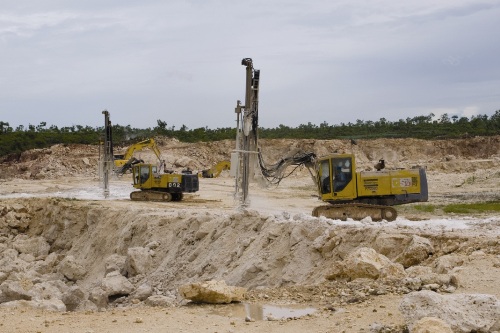
Quarrying activity at UTSG’s facility is steady at two shifts per day, seven days a week.
The mine maintains a 6 m to 9 m bench and exercises 2.75 m spacing and 2.75 m burden. Each drill rig is expected to drill 480 m per day using Atlas Copco Secoroc 3.5 inch bits.
In this soft rock formation, the service life of each bit is roughly six months, averaging 72,000 meters per bit. The quarry’s current working area is 797,44 hectares and operates at an 80 m depth to sea level.
Conclusion
According to Haryanto, Managing Supervisor for Maintenance, the high rate of availability is attributable to the good relationship with Atlas Copco through good communication. The interaction between Atlas Copco, the maintenance department, and the logistics department are the key components of that relationship.
About Atlas Copco
In close cooperation with customers and business partners, and with more than 130 years of experience, Atlas Copco innovates for sustainable productivity.
- The products and services include compressors, expanders and air treatment systems, construction and mining equipment, power tools and assembly systems.
- Atlas Copco's customers are located almost everywhere on the globe. Though to its customers Atlas Copco is a local company of neighbours and friends, each Atlas Copco center is supported by the Atlas Copco Group enterprise with a worldwide network of resources.
- Headquartered in Stockholm, Sweden, the Group’s global reach spans more than 170 markets with sales operations in more than 80 countries. In the other countries, the products are marketed through distributors and service networks.
- The Group has production facilities in more than 20 countries. Manufacturing is mainly concentrated in Belgium, Sweden, Germany, the United States, India and China.
Atlas Copco’s objective to be a responsible corporate citizen in each market. By making a positive impact in the economic, environmental and social aspects each market and through employee pride in the Group’s values.
With a tradition of innovation dating back to the Group’s founding in 1873, the core business remains much the same, with today's equipment delivering an unparalleled level of efficiency.
Atlas Copco’s vision is to become and to remain First in Mind-First in Choice® for its stakeholders, which is also the driving force of the Group’s corporate responsibility strategy.
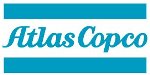
This information has been sourced, reviewed and adapted from materials provided by Atlas Copco.
For more information on this source, please visit Atlas Copco.