In a recent article published in the Chemical Engineering Journal, researchers proposed an alternative process involving sodium hydroxide (NaOH) roasting followed by water leaching to enhance lithium (Li) extraction efficiency from spodumene. The research focuses on optimizing the roasting parameters, understanding the reaction kinetics, and assessing the leaching process, aiming to develop a more sustainable and cost-effective method for lithium beneficiation.
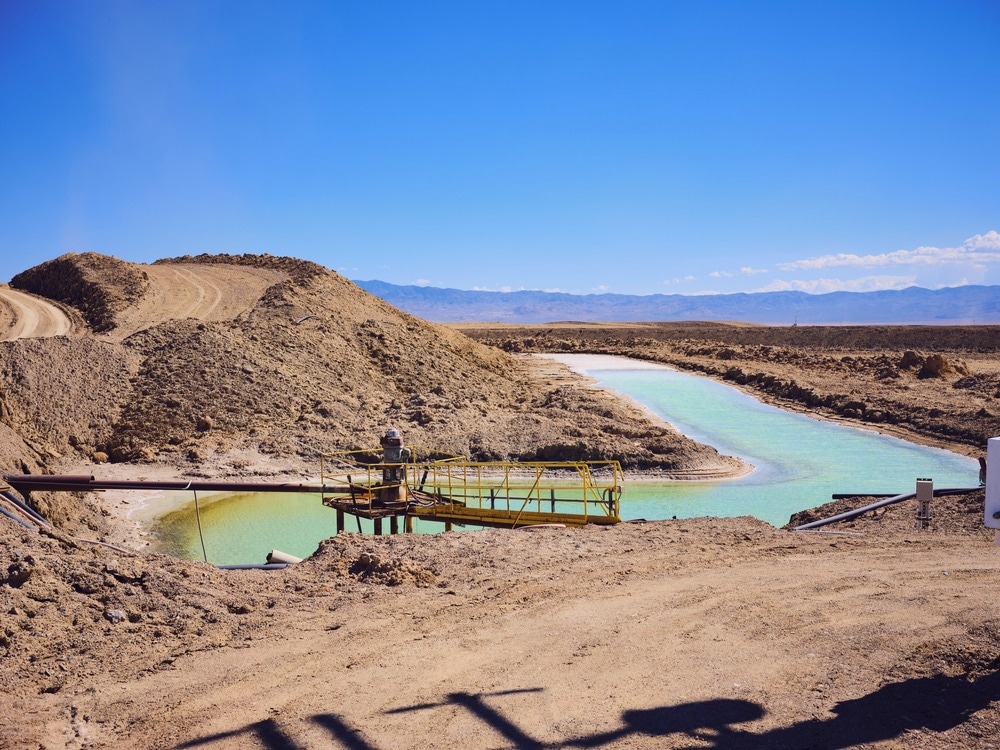
Image Credit: Cavan-Images/Shutterstock.com
Background
Spodumene (LiAlSi₂O₆), a lithium-bearing pyroxene mineral, exists predominantly in α- and β-forms. The α-form, which is less reactive, requires high-temperature treatments to convert into a more reactive β-phase suitable for leaching.
Conventional roasting methods typically operate at temperatures exceeding 1000 °C, producing sizable energy consumption and environmental concerns.
Recent advances have explored alkali roasting—particularly with NaOH—to facilitate lithium extraction at comparatively lower temperatures.
Previous studies indicate that the melting point of NaOH (~318 °C) plays a critical role in reaction efficiency, with optimal lithium recovery often occurring near or below this temperature.
The mechanisms underlying these processes involve complex solid-state reactions, diffusion of alkali into silicate matrices, and subsequent water leaching to solubilize lithium. A comprehensive understanding of reaction kinetics, process parameters, and their effects on lithium recovery is essential for refining process conditions and scaling up.
The Current Study
The experimental methodology centers on an alkali roasting and water leaching sequence, systematically optimized to maximize lithium recovery. Initially, spodumene concentrates were subjected to roasting with NaOH under controlled conditions, varying key parameters such as temperature, roasting duration, and particle size.
Roasting temperatures explored ranged from 250 °C to 600 °C, with particular emphasis on the melting point of NaOH. Kinetic studies were performed using a thermogravimetric analyzer (TGA), which measured the reaction rate and activation energy, revealing that the NaOH-spodumene reaction at ~325 °C follows a reaction rate of 0.065 mg/min with a high activation energy of 212 kJ/mol.
These insights underscored the importance of dwelling time, with two hours identified as optimal, ensuring complete reaction without excessive energy consumption. Post-roasting, the residues were cooled and prepared for leaching, which involved varying the solid-to-liquid ratio, stirring rate, and temperature to optimize lithium dissolution.
The water leaching process was conducted in laboratory-scale reactors, with the residue from roasting being mixed with ultrapure deionized water at different solid-to-liquid ratios, primarily 1%, 2%, 5%, 10%, and higher, to study the influence on Li recovery.
Stirring rates ranged from 0 rpm (no agitation) to 400 rpm, with 200 rpm identified as optimal for efficient dispersion and mass transfer. The temperature's effect was also examined, from room temperature (~23 °C) to elevated temperatures such as 60 °C and 90 °C, recognizing the typically exothermic nature of alkali-silicate reactions.
Elemental concentrations in leachates were analyzed using inductively coupled plasma atomic emission spectroscopy (ICP-AES) and ICP-mass spectrometry (ICP-MS), ensuring precise quantification of lithium and other elements. The kinetic behavior during leaching was monitored by extracting samples at predefined intervals, allowing characterization of the reaction dynamics and diffusion mechanisms.
Results and Discussion
The experimental findings demonstrate that the highest lithium recovery during roasting occurred at approximately 325 °C, with a Li recovery of about 82% when roasted for around two hours. This temperature aligns closely with NaOH’s melting point, facilitating a significant increase in reaction kinetics due to the formation of a melt that enhances diffusion of NaOH into the spodumene matrix.
Kinetic analysis revealed that the reaction adheres to a high activation energy of 212 kJ/mol, emphasizing the need for sufficient dwelling time during roasting. Reaction rates during roasting peaked at approximately 0.065 mg/min at 325 °C, with the process reaching a near-peak lithium recovery within 10 minutes in some conditions. This rapid kinetics indicates that prolonged roasting beyond optimal durations offers diminishing returns and may lead to energy wastage.
Leaching studies revealed that the optimal solid-to-liquid ratio was 1%, maintaining a high concentration gradient for lithium dissolution while minimizing residual solid costs.
Stirring at 200 rpm was sufficient to ensure uniform dispersion without excess energy input, with little difference observed at higher stirring rates. Temperature studies indicated that increasing water temperature beyond 60 °C led to decreased lithium recovery, likely due to the exothermic backward reactions favoring lithium re-precipitation or forming insoluble phases. Such findings emphasized that room temperature leaching (around 23 °C) is sufficient under optimized conditions, reducing additional energy needs.
Conclusion
This comprehensive study establishes that sodium hydroxide roasting followed by water leaching can effectively extract lithium from spodumene with high efficiency at relatively lower temperatures than conventional methods.
By understanding the fundamental reaction mechanisms and kinetics, this methodology offers a promising avenue for sustainable lithium extraction, enabling the industry to move toward greener and more cost-effective practices. Future work should focus on scaling these laboratory insights to industrial applications, considering process integration, waste management, and economic analysis to realize the potential of this alternative lithium beneficiation process fully.
Source:
Subasinghe H.C.S., Rezaee, M. (2025). Direct lithium extraction from α-spodumene using NaOH roasting and water leaching. Chemical Engineering Journal, 505, 159661. DOI: 10.1016/j.cej.2025.159661, https://www.sciencedirect.com/science/article/pii/S1385894725004607?via%3Dihub