In a recent article published in the journal Scientific Reports, researchers investigated the efficacy of incorporating polypropylene fibers into concrete mixes and applies external surface treatments—namely polyurethane and asphalt coatings—to bolster resistance against acid attack, water ingress, and erosive wear.
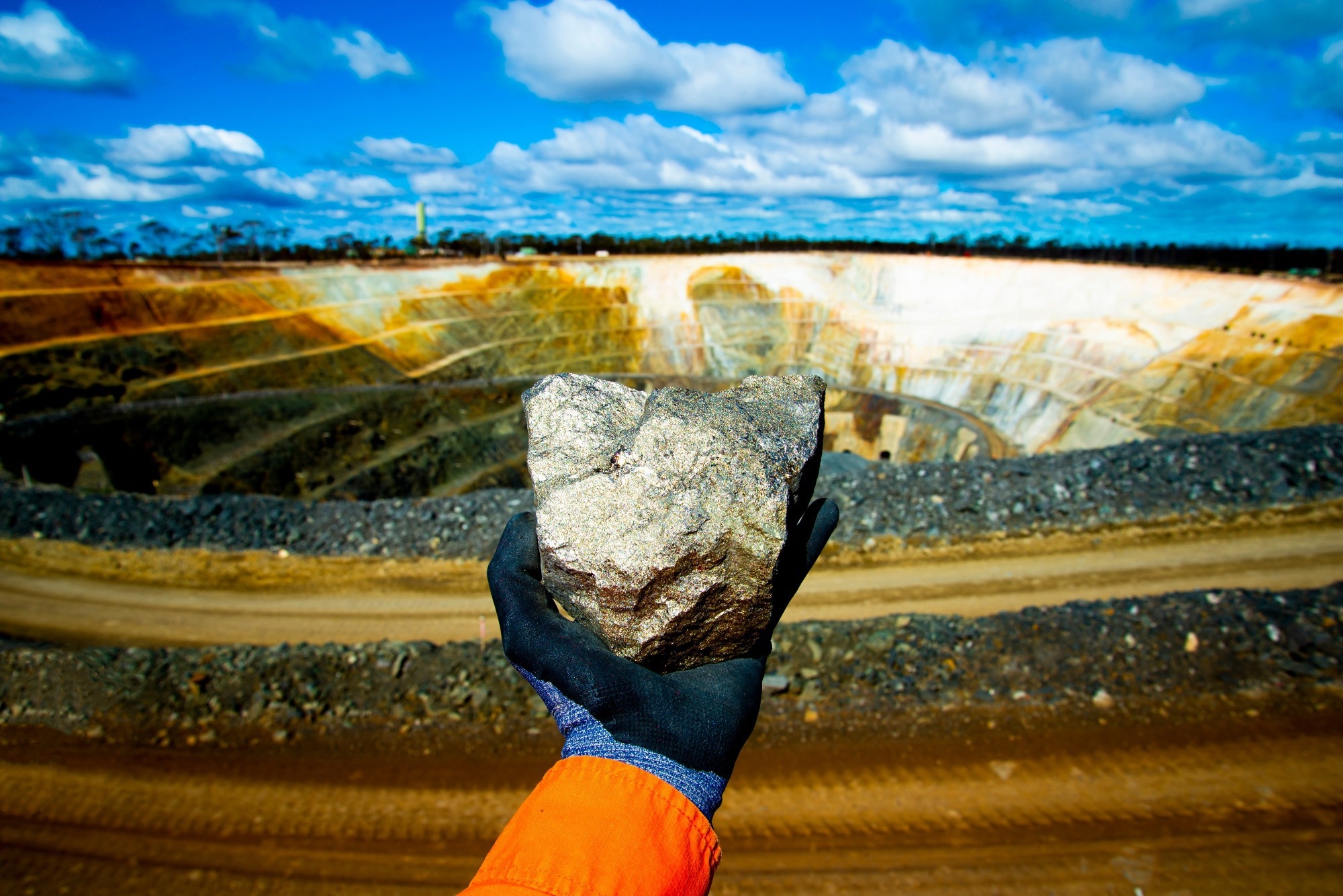
Image Credit: Adwo/Shutterstock.com
Background
Concrete durability in sulphide mining environments is compromised predominantly by the low pH levels and the presence of sulphates and magnesium, all of which induce chemical and physical deterioration.
The oxidation of pyrite (FeS₂), common in such environments, produces sulphates and ferrous ions, which further react and accelerate the degradation process. Acidophilic bacteria play a significant role in this process by facilitating oxidation reactions that generate additional acidity and sulphate ions. These factors reduce the lifespan of concrete structures, leading to mass loss, spalling, cracking, and loss of mechanical properties.
Traditionally, improving durability has included adding supplementary cementitious materials such as silica fume, which can fill pores and reduce permeability, or employing surface coatings as barriers to chemical ingress.
Fiber reinforcement, specifically polypropylene fibers, has been recognized for improving tensile and cracking resistance, but its effectiveness against chemical and microbial attacks in such harsh environments remains an area of active research. As such, the combination of internal reinforcement and external protective layers offers a promising strategy for extending service life.
The Current Study
The experimental approach involved designing a mass concrete mix with specific characteristics aligned with current building codes, including a minimum compressive strength of 35 MPa, a cement content of 325 kg/m³, and a water-to-cement ratio not exceeding 0.45.
The study incorporated polypropylene fibers at a concentration of 3.4 kg/m³, a level chosen based on prior literature indicating an optimal point for tensile strength improvements without adversely affecting workability.
The concrete specimens were prepared and subjected to various tests to evaluate their mechanical and durability performance. The primary mechanical tests included tensile and compressive strength assessments.
To simulate the aggressive conditions of sulphide mining, the specimens underwent water immersion tests, Slake durability tests, and abrasion resistance assessments using an abrasive blast machine with alumina grit.
External surface treatments consisted of applying polyurethane and asphalt coatings, chosen for their known chemical resistance and capacity to inhibit water and sulphate ingress.
Specimens with these coatings were cured and then subjected to the same durability tests as uncoated samples. The Slake test involved cyclic immersion and disintegration assessments, measuring the percentage loss in mass and the degree of surface degradation after exposure times of 20 and 120 minutes.
The abrasion resistance was evaluated via sandblasting, measuring material loss and disintegrated particle size distribution. To analyze water ingress, water penetration depth tests were also performed on coated and uncoated specimens. Additionally, tests quantified the volume loss of specimens post-treatment, and microscopic examinations assessed surface integrity and coatings adherence.
Results and Discussion
The incorporation of polypropylene fibers yielded notable improvements in the tensile strength of the concrete. The maximum tensile strength was observed at a fiber concentration of approximately 3.4 kg/m³, registering an increase of about 8% relative to unreinforced specimens. Interestingly, the fibers also contributed significantly to reducing the internal porosity and water permeability, with water penetration depths halving compared to the reference. Although the enhancement in compressive strength was modest, a peak was identified at a 1.7 kg/m³ fiber dosage, aligning with prior research indicating an optimum fiber content beyond which deterioration may occur due to fiber clustering or increased porosity.
External surface treatments proved highly effective in mitigating water ingress and erosion. The polyurethane coating demonstrated superior durability, achieving a zero-water penetration depth and a Slake index of nearly 99.55% after 120 minutes, reflecting minimal disintegration. Asphalt coatings also significantly improved resistance, with a Slake index of 98.99%, indicating strong performance against chemical attack and mechanical wear. The abrasion tests confirmed that coated specimens experienced negligible mass loss and disintegration, confirming the coatings’ barrier effect. When combined with fiber reinforcement, the protective effects were amplified, leading to further reductions in mass loss and surface degradation.
Conclusion
This comprehensive investigation confirms that combining internal fiber reinforcement with external surface treatments significantly enhances the durability of concrete subjected to the aggressive conditions characteristic of sulphide mining environments. The findings demonstrate that polypropylene fibers at a concentration of around 3.4 kg/m³ effectively improve tensile strength and reduce water permeability, crucial factors for resisting chemical ingress and physical wear.
External coatings, particularly polyurethane, serve as an efficient barrier against water penetration, microbial attack, and erosion, maintaining surface integrity over prolonged exposure periods. The synergy between fiber reinforcement and protective coatings results in a concrete system capable of withstanding the corrosive influence of acid mine drainage, sulphates, and bacterial activity, thus extending service life and reducing maintenance costs.
Source:
Davila J.M., Rodriguez-Gomez C., et al. (2025). Use of fibres and surface treatment to improve the durability of concrete affected by sulphide mining. Scientific Reports 15, 25090. DOI: 10.1038/s41598-025-10855-9, https://www.nature.com/articles/s41598-025-10855-9